Manufacturing method for bearing ball
A manufacturing method and technology of bearing balls, which are applied in the mechanical field and can solve problems such as complex processes, hidden safety hazards, and stalling
- Summary
- Abstract
- Description
- Claims
- Application Information
AI Technical Summary
Problems solved by technology
Method used
Examples
Embodiment 1
[0015] A method for manufacturing bearing balls, comprising the following steps:
[0016] 1), material selection: select the material, and then pier rough, forging rough processing.
[0017] 2) Then, put the material into a 300-ton press and perform hot forging at a temperature of 1000°C.
[0018] 3) Then perform annealing treatment, using an oxygen-free annealing furnace, the annealing temperature is 850°C, keep warm for 3 hours, and cool down.
[0019] 4) After cooling, carry out cold rolling treatment, and then put it into a quenching furnace for quenching at a temperature of 100°C.
[0020] 5) Put it into a melting furnace for melting, and melt water to make a plurality of small ingots.
[0021] 6), put into the mill and grind into balls.
Embodiment 2
[0023] A method for manufacturing bearing balls, comprising the following steps:
[0024] 1), material selection: select the material, and then pier rough, forging rough processing.
[0025] 2), and then put the material into a 300-ton press, and carry out hot forging at a temperature of 1200°C.
[0026] 3) Then annealing treatment is carried out in an oxygen-free annealing furnace, the annealing temperature is 890°C, the temperature is kept for 6 hours, and then cooled.
[0027] 4) After cooling, carry out cold rolling treatment, and then put it into a quenching furnace for quenching at a temperature of 200°C.
[0028] 5) Put it into a melting furnace for melting, and melt water to make a plurality of small ingots.
[0029] 6), put into the mill and grind into balls.
Embodiment 3
[0031] A method for manufacturing bearing balls, comprising the following steps:
[0032] 1), material selection: select the material, and then pier rough, forging rough processing.
[0033] 2) Then, put the material into a 300-ton press and perform hot forging at a temperature of 1100°C.
[0034] 3) Then perform annealing treatment, using an oxygen-free annealing furnace, the annealing temperature is 840°C, keep warm for 4 hours, and cool down.
[0035] 4) After cooling, carry out cold rolling treatment, and then put into a quenching furnace for quenching at a temperature of 150°C.
[0036] 5) Put it into a melting furnace for melting, and melt water to make a plurality of small ingots.
[0037] 6), put into the mill and grind into balls.
PUM
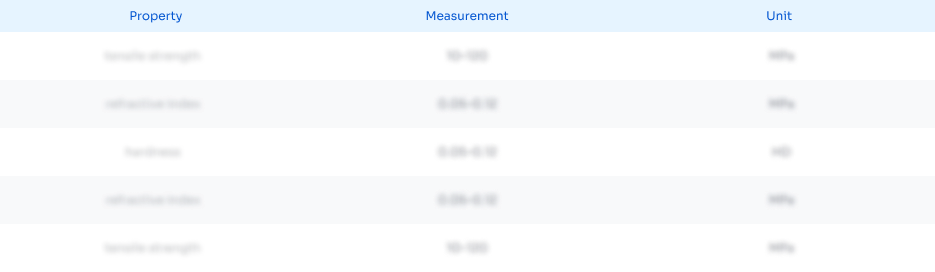
Abstract
Description
Claims
Application Information

- R&D Engineer
- R&D Manager
- IP Professional
- Industry Leading Data Capabilities
- Powerful AI technology
- Patent DNA Extraction
Browse by: Latest US Patents, China's latest patents, Technical Efficacy Thesaurus, Application Domain, Technology Topic, Popular Technical Reports.
© 2024 PatSnap. All rights reserved.Legal|Privacy policy|Modern Slavery Act Transparency Statement|Sitemap|About US| Contact US: help@patsnap.com