Modification method for semi-dry sintering flue gas desulfurization ash
A technology for sintering flue gas and desulfurization ash, which is applied in separation methods, chemical instruments and methods, and separation of dispersed particles, can solve the problems of content reduction and comprehensive utilization of desulfurization ash, and achieve content reduction, economic benefits and social benefits. , the effect of reducing production costs
- Summary
- Abstract
- Description
- Claims
- Application Information
AI Technical Summary
Problems solved by technology
Method used
Image
Examples
Embodiment 1
[0025] (1). Use a 100-mesh sieve to sieve the semi-dry sintering flue gas desulfurization ash, and continue to sieve the remaining large particles after grinding until all of them pass through a 100-mesh sieve to obtain desulfurization ash I;
[0026] (2) Soak the desulfurized ash I obtained in step (1) in deionized water, wherein the ratio of the mass of desulfurized ash I to the volume of deionized water is 1g: 20ml; heat to 40°C and keep warm for 4h; filter, and the filtrate is Chloride salt solution, the filter residue is desulfurization ash II;
[0027] (3) Weigh 35g of oxalic acid, add 665ml of deionized water, heat to 60°C, and keep it warm for 15min to obtain an oxalic acid solution with a mass fraction of 5%;
[0028] (4) Soak the desulfurized ash II obtained in step (2) in the oxalic acid solution obtained in step (3), wherein the ratio of the mass of desulfurized ash II to the volume of the oxalic acid solution is 3g: 20ml; heat to 50°C, keep stirring 8h, in which ...
Embodiment 2
[0034] (1). Use a 100-mesh sieve to sieve the semi-dry sintering flue gas desulfurization ash, and continue to sieve the remaining large particles after grinding until all of them pass through a 100-mesh sieve to obtain desulfurization ash I;
[0035] (2) Soak the desulfurized ash I obtained in step (1) in deionized water, wherein the ratio of the mass of desulfurized ash I to the volume of deionized water is 1g: 10ml; heat to 60°C and keep warm for 3h; filter, and the filtrate is Chloride salt solution, the filter residue is desulfurization ash II;
[0036] (3) Weigh 70g of oxalic acid, add 630ml of deionized water, heat to 70°C, and keep it warm for 12min to obtain an oxalic acid solution with a mass fraction of 10%;
[0037] (4) Soak the desulfurized ash II obtained in step (2) in the oxalic acid solution obtained in step (3), wherein the ratio of the mass of desulfurized ash II to the volume of the oxalic acid solution is 1g: 20ml; heat to 60°C, keep stirring 5h, wherein ...
Embodiment 3
[0043] (1). Use a 100-mesh sieve to sieve the semi-dry sintering flue gas desulfurization ash, and continue to sieve the remaining large particles after grinding until all of them pass through a 100-mesh sieve to obtain desulfurization ash I;
[0044] (2) Soak the desulfurized ash I obtained in step (1) in deionized water, wherein the ratio of the mass of desulfurized ash I to the volume of deionized water is 1g︰40ml; heat to 70°C and keep warm for 2h; filter, and the filtrate is Chloride salt solution, the filter residue is desulfurization ash II;
[0045] (3) Weigh 140g of oxalic acid, add 560ml of deionized water, heat to 80°C, and keep it warm for 10min to obtain an oxalic acid solution with a mass fraction of 20%;
[0046] (4) Soak the desulfurized ash II obtained in step (2) in the oxalic acid solution obtained in step (3), wherein the ratio of the mass of desulfurized ash II to the volume of the oxalic acid solution is 1g: 40ml; heat to 50°C, keep stirring 6h, in which...
PUM
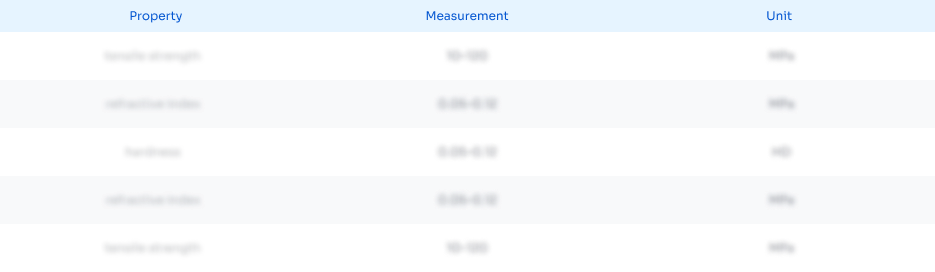
Abstract
Description
Claims
Application Information

- R&D
- Intellectual Property
- Life Sciences
- Materials
- Tech Scout
- Unparalleled Data Quality
- Higher Quality Content
- 60% Fewer Hallucinations
Browse by: Latest US Patents, China's latest patents, Technical Efficacy Thesaurus, Application Domain, Technology Topic, Popular Technical Reports.
© 2025 PatSnap. All rights reserved.Legal|Privacy policy|Modern Slavery Act Transparency Statement|Sitemap|About US| Contact US: help@patsnap.com