Dehydrogenation method
A dehydrogenation and steel type technology, applied in the field of dehydrogenation, can solve the problems of manganese alloy moisture, reduced lubricity of mold slag, increased heat transfer resistance, etc., to reduce manganese loss, reduce hydrogen content, and avoid billet sticking The effect of breakout
- Summary
- Abstract
- Description
- Claims
- Application Information
AI Technical Summary
Problems solved by technology
Method used
Examples
Embodiment 1
[0014] The present embodiment is carried out on a 180-ton RH refining furnace, and the highest vacuum degree is 80Pa. The smelted steel is Mn13, the liquidus temperature is 1389°C, and the mass percentage of the chemical composition of the finished product is:
[0015] C 0.90-1.20; Si 0.30-0.80; Mn 11.00-14.00; P≤0.035;
[0016] S≤0.030; Cr≤1.00; Mo≤0.10; V≤0.10;
[0017] The rest is Fe and unavoidable impurities.
[0018] Before dehydrogenation treatment, molten steel is 183t, temperature is 1511℃, ladle space is 350mm, slag thickness is 80mm, fixed hydrogen is 6ppm, chemical composition mass percentage:
[0019] C 1.03; Si 0.38; Mn 13.11; P 0.005; S 0.004;
[0020] Cr 0.85; Mo 0.06; V 0.07; the rest is Fe and unavoidable impurities.
[0021] Vacuumize, cycle for 2 minutes, and the vacuum degree reaches 5×10 2 Pa, at vacuum degree 5×10 2 Under Pa, treat for 25min.
[0022] After treatment, the hydrogen is fixed, the hydrogen content of the molten steel is 1.8ppm, the t...
Embodiment 2
[0027] The present embodiment is carried out on a 90-ton RH refining furnace with a maximum vacuum of 50 Pa. The smelted steel is 20Mn23AlV, the liquidus temperature is 1421°C, and the mass percentage of the chemical composition of the finished product is:
[0028] C 0.14-0.20; Si≤0.50; Mn 21.50-25.00; P≤0.030; S≤0.030;
[0029] Al 1.50-2.50; V 0.05-0.10; the rest is Fe and unavoidable impurities.
[0030] Before dehydrogenation treatment, molten steel is 85t, temperature is 1525°C, ladle space is 400mm, slag thickness is 100mm, fixed hydrogen is 4.3ppm, chemical composition mass percentage:
[0031] C 0.19; Si 0.11; Mn 22.07; P 0.006; S 0.002; Al 2.39;
[0032] V 0.06; the rest is Fe and unavoidable impurities.
[0033] Vacuumize, cycle for 1.5min, and the vacuum degree reaches 10×10 2 Pa, in a vacuum of 10×10 2 Under Pa, treat for 18min.
[0034] After treatment, hydrogen was fixed, the hydrogen content of molten steel was 2.1ppm, the temperature was 1490°C, and the ma...
PUM
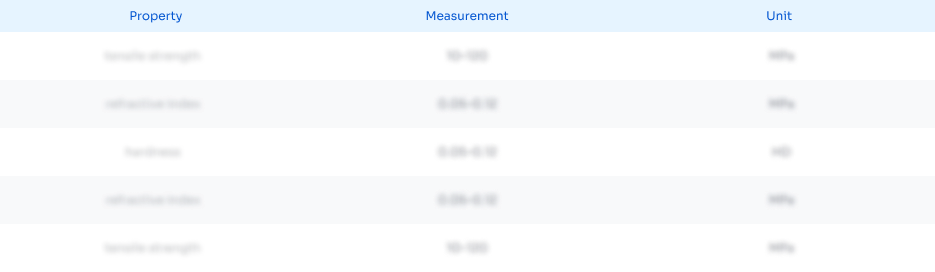
Abstract
Description
Claims
Application Information

- R&D
- Intellectual Property
- Life Sciences
- Materials
- Tech Scout
- Unparalleled Data Quality
- Higher Quality Content
- 60% Fewer Hallucinations
Browse by: Latest US Patents, China's latest patents, Technical Efficacy Thesaurus, Application Domain, Technology Topic, Popular Technical Reports.
© 2025 PatSnap. All rights reserved.Legal|Privacy policy|Modern Slavery Act Transparency Statement|Sitemap|About US| Contact US: help@patsnap.com