Method for manufacturing box shell of large special-shaped low-pressure turbine used for aircraft engine
A low-pressure turbine, aero-engine technology, applied in engine components, mechanical equipment, etc., can solve problems such as the stability defect of the gate housing, the low utilization rate of production materials, and the incomplete flow line of forgings, so as to ensure consistency and stability. The effect of high stability, short manufacturing cycle and complete metal streamline
- Summary
- Abstract
- Description
- Claims
- Application Information
AI Technical Summary
Problems solved by technology
Method used
Image
Examples
Embodiment 1
[0034] (1) Cutting and heating:
[0035] The GH4169 alloy billet is chamfered to R20mm, and the billet is heated by three-stage heating at a heating temperature of 845°C, 975°C, and 1015°C, and the holding time of each heating stage is calculated according to 6min / 10mm;
[0036] (2) Upsetting, punching, and expanding holes:
[0037] Upsetting the blank in the axial direction until the length is 44% of the original length, punching with a punch, expanding the hole until the hole diameter at one end is 72% of the hole diameter at the other end;
[0038] (3) Horse frame reaming:
[0039] Carry out reaming so that the inner diameter of the large hole is 80% of the outer diameter, the inner diameter of the small hole is 75% of the outer diameter, and the inner diameter of the small hole is 55% of the inner diameter of the large hole;
[0040] (4) Forging forming:
[0041] The forming size of the forging is that the radius of the large hole is 90% of the outer radius of the large...
Embodiment 2
[0043] (1) Cutting and heating:
[0044] The GH4169 alloy blank is chamfered to R20mm, and the blank is heated by three-stage heating at a heating temperature of 855°C, 985°C, and 1025°C, and the holding time of each heating section is calculated as 6min / 10mm;
[0045] (2) Upsetting, punching, and expanding holes:
[0046] Upsetting the blank in the axial direction until the length is 46% of the original length, punching with a punch, expanding the hole until the hole diameter at one end is 74% of the hole diameter at the other end;
[0047] (3) Horse frame reaming:
[0048] Carry out horse frame reaming so that the inner diameter of the large hole is 85% of the outer diameter, the inner diameter of the small hole is 80% of the outer diameter, and the inner diameter of the small hole is 60% of the inner diameter of the large hole;
[0049] (4) Forging forming:
[0050] The forming size of the forging is that the radius of the large hole is 95% of the outer radius of the lar...
Embodiment 3
[0052] (1) Cutting and heating:
[0053] The GH4169 alloy billet is chamfered to R20mm, and the billet is heated in a three-stage heating method with a heating temperature of 850°C, 980°C, and 1020°C, and the holding time of each heating section is calculated according to 6min / 10mm;
[0054] (2) Upsetting, punching, and expanding holes:
[0055] Upsetting the blank in the axial direction until the length is 45% of the original length, punching with a punch, expanding the hole until the diameter of one end hole is 73% of the other end hole diameter;
[0056] (3) Horse frame reaming:
[0057]Carry out saddle reaming so that the inner diameter of the large hole is 82.5% of the outer diameter, the inner diameter of the small hole is 77.5% of the outer diameter, and the inner diameter of the small hole is 57.5% of the inner diameter of the large hole;
[0058] (4) Forging forming:
[0059] The forming size of the forging is that the radius of the large hole is 92.5% of the outer...
PUM
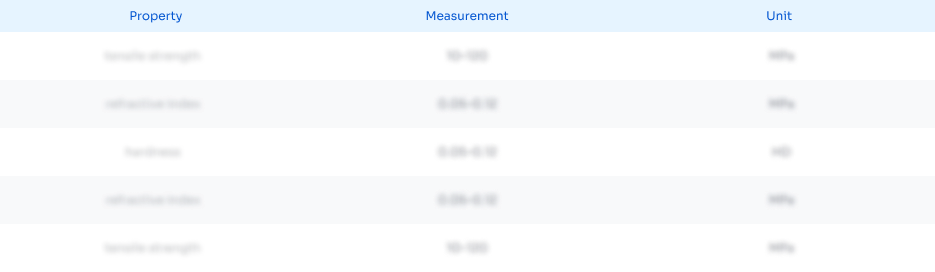
Abstract
Description
Claims
Application Information

- R&D Engineer
- R&D Manager
- IP Professional
- Industry Leading Data Capabilities
- Powerful AI technology
- Patent DNA Extraction
Browse by: Latest US Patents, China's latest patents, Technical Efficacy Thesaurus, Application Domain, Technology Topic, Popular Technical Reports.
© 2024 PatSnap. All rights reserved.Legal|Privacy policy|Modern Slavery Act Transparency Statement|Sitemap|About US| Contact US: help@patsnap.com