System and method for recovering exhaust gas in olefin polymer production
A recovery system, a technology for olefin polymerization, applied in ethylene production, chemical instruments and methods, separation methods, etc., can solve the problems of low tail gas pressure, only discharge, unable to achieve efficient hydrocarbon recovery and purging gas recycling at the same time, etc. Achieve the effect of low energy consumption and high recovery rate
- Summary
- Abstract
- Description
- Claims
- Application Information
AI Technical Summary
Problems solved by technology
Method used
Image
Examples
example 1
[0068] use as Figure 7 The exhaust gas recovery device shown in the figure treats the exhaust gas of a gas-phase polyethylene plant with an annual output of 400,000 tons of polyethylene resin, and recovers low-carbon hydrocarbons and other substances in the exhaust gas. The exhaust gas recovery device includes: a devolatilization device A, a gas compression device B, a first heat exchange device C, a first gas-liquid separation device D, a first gas separation device E, a second heat exchange device F, a second Gas-liquid separation device G, third heat exchange device H, gas expansion device I. Among them, the first gas separation device uses a membrane system to separate the hydrogen in the exhaust gas; the second gas separation device consists of the second heat exchange device F, the second gas-liquid separation device G, the third heat exchange device H, and the gas expansion device I composition. Gas expansion device 1 is a turbo expander.
[0069] The specific proce...
example 2
[0075] use as Figure 8 The exhaust gas recovery device shown in the figure treats the exhaust gas of a gas-phase polyethylene plant with an annual output of 400,000 tons of polyethylene resin, and recovers low-carbon hydrocarbons and other substances in the exhaust gas. The exhaust gas recovery device includes: a devolatilization device A, a gas compression device B, a first heat exchange device C, a first gas-liquid separation device D, a first gas separation device E, a second heat exchange device F, a second Gas-liquid separation device G, third heat exchange device H, third gas-liquid separation device I, fourth heat exchange device J, gas expansion device K. Among them, the first gas separation device uses a membrane system to separate the hydrogen in the exhaust gas; the second gas separation device consists of the second heat exchange device F, the second gas-liquid separation device G, the third heat exchange device H, and the third gas-liquid separation device. The ...
PUM
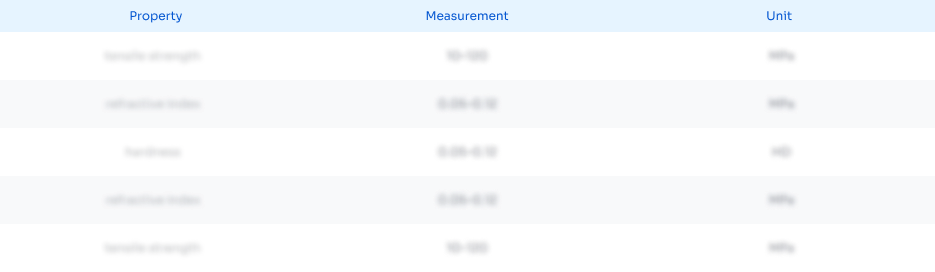
Abstract
Description
Claims
Application Information

- Generate Ideas
- Intellectual Property
- Life Sciences
- Materials
- Tech Scout
- Unparalleled Data Quality
- Higher Quality Content
- 60% Fewer Hallucinations
Browse by: Latest US Patents, China's latest patents, Technical Efficacy Thesaurus, Application Domain, Technology Topic, Popular Technical Reports.
© 2025 PatSnap. All rights reserved.Legal|Privacy policy|Modern Slavery Act Transparency Statement|Sitemap|About US| Contact US: help@patsnap.com