Method, device and system for controlling PMSM (Permanent Magnet Synchronous Motor) to put into operation again at belt speed
A permanent magnet synchronous motor, re-input technology, applied in the control system, motor control, vector control system and other directions, can solve the problem of isolation contactor input logic without considering the re-operation, unable to ensure the stable operation of the closed control system, etc.
- Summary
- Abstract
- Description
- Claims
- Application Information
AI Technical Summary
Problems solved by technology
Method used
Image
Examples
Embodiment 1
[0111] see image 3 , which is a flow chart of Embodiment 1 of the control method for re-starting the permanent magnet synchronous motor with speed provided by the present invention.
[0112] First, the working principle on which the present invention is based is introduced.
[0113] It can be seen from formula (1) that as long as the speed ω e is high enough, the back EMF E 0 will be higher than the intermediate DC side voltage U of the inverter dc , if the belt-speed re-commissioning operation is performed at this time and the isolation contactor is switched on, the PMSM will reversely charge the DC side of the inverter. The charged voltage amplitude of the capacitor on the DC side of the inverter may be higher than the safe allowable value of the capacitor, causing damage to the capacitor.
[0114] Therefore, re-injection with speed is not possible at all speeds of the PMSM, and it needs to be judged according to the rotational speed of the PMSM corresponding to the re-...
Embodiment 2
[0130] The method of obtaining the rotor position angle by using a short-circuit method provided by the present invention when the PMSM is in the medium-high speed section will be described in detail below in conjunction with the accompanying drawings.
[0131] see Figure 4 , which is a flow chart of the primary short-circuit method in the middle and high-speed section provided by the present invention.
[0132] Due to the existence of the back electromotive force when the PMSM is idling, if the three phases of the PMSM are short-circuited, the three-phase short-circuit current must contain the position information of the PMSM rotor, so the short-circuit method can be used to obtain the rotor position angle.
[0133] S401: applying a zero-voltage vector to make the permanent magnet synchronous motor in a short-circuit state;
[0134] It should be noted that there are two zero voltage vectors, one is and That is, by applying these two different zero-voltage vectors, all t...
Embodiment 3
[0154] The following introduces that the present invention uses the INFORM method to obtain the rotor position angle when it is in the low-speed stage.
[0155] see Figure 6 , which is a flow chart for calculating the rotor position angle using the INFORM method provided by the present invention.
[0156] First, the basic principle of the INFORM method is introduced: apply voltage space vectors to the motor terminals from different directions, and estimate the rotor position by measuring their different current responses.
[0157] The basic principle used is: the magnetic circuit of the motor has a salient polarity, and the inductance value of the stator winding is a function of the rotor position, so the current response generated by the voltage space vector at different positions must contain the rotor position information.
[0158] Since the applied voltage space vector is a high-frequency voltage signal, and the current response is also a high-frequency signal, the motor...
PUM
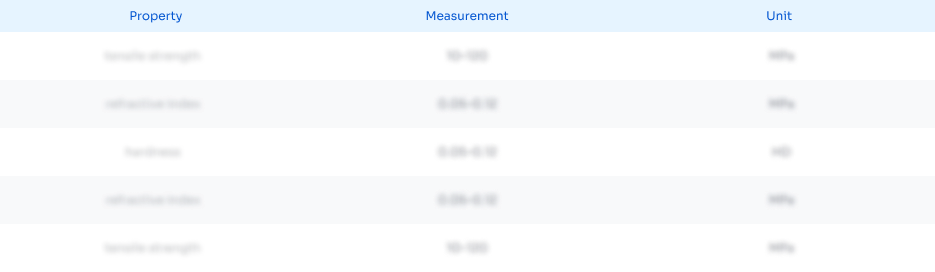
Abstract
Description
Claims
Application Information

- R&D
- Intellectual Property
- Life Sciences
- Materials
- Tech Scout
- Unparalleled Data Quality
- Higher Quality Content
- 60% Fewer Hallucinations
Browse by: Latest US Patents, China's latest patents, Technical Efficacy Thesaurus, Application Domain, Technology Topic, Popular Technical Reports.
© 2025 PatSnap. All rights reserved.Legal|Privacy policy|Modern Slavery Act Transparency Statement|Sitemap|About US| Contact US: help@patsnap.com