Low-wear brush type seal
A brush-type sealing, low-wear technology, applied in the direction of preventing leakage, engine components, machines/engines, etc., can solve the problems of rotor friction and wear friction heat, increasing the gap between the brush wire bundle and the rotor, and reducing the reliability of the brush wire, etc. Achieve the effect of improving reliability, improving stability and safety, improving friction and wear and heating
- Summary
- Abstract
- Description
- Claims
- Application Information
AI Technical Summary
Problems solved by technology
Method used
Image
Examples
Embodiment 1
[0024] 3 is a schematic diagram of Embodiment 1 of the present invention. The brush seal structure includes a front baffle 1, a rear baffle 2, and a brush filament bundle 3. The root 4 of the brush filament bundle 3 is enclosed by the front baffle 1 and the rear baffle 2. The clamped brush filament bundle 3 is "blown down" under the upstream pressure to contact the rotor 5 to achieve a sealing effect and prevent the sealed fluid medium from leaking from upstream to downstream. Wherein, the brush filaments in the brush filament area 3 are not flush in the radial direction of the rotor 5, and the lengths of several downstream brush filaments of the brush filament bundle 3 are shorter than the upstream brush filaments, that is, from the axial direction of the rotor 5 to - Viewed on the radial plane, there is a gap 31 at the downstream free end of the brush filament bundle 3; the gap 31 is triangular when viewed on the axial-radial plane of the rotor 5 (refer to FIG. 3 ), and the a...
Embodiment 2
[0026] Figure 4 is a schematic diagram of Embodiment 2 of the present invention. The brush seal structure includes a front baffle 1, a rear baffle 2, and a brush filament bundle 3, and the root 4 of the brush filament bundle 3 is clamped by the front baffle 1 and the rear baffle 2. Hold, the brush filament bundle 3 is "blown down" under the upstream pressure to contact the rotor 5 to play a sealing effect, preventing the sealed fluid medium from leaking from upstream to downstream. Wherein, the brush filaments in the brush filament area 3 are not flush in the radial direction of the rotor 5, and the lengths of several downstream brush filaments of the brush filament bundle 3 are shorter than the upstream brush filaments, that is, from the axial direction of the rotor 5 to - Viewed on the radial plane, there is a gap 31 at the downstream free end of the brush filament bundle 3; the gap 31 is rectangular when viewed on the axial-radial plane of the rotor 5 (refer to FIG. 4 ), and...
PUM
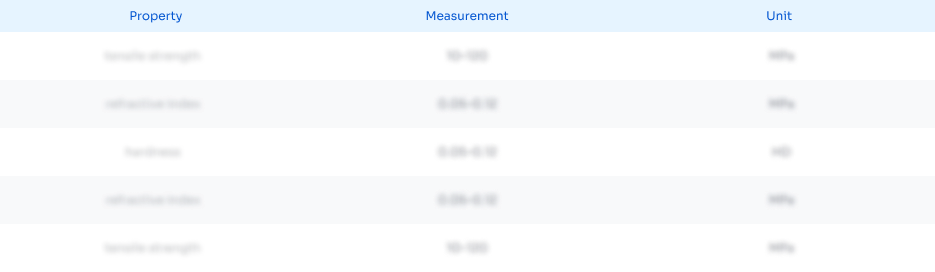
Abstract
Description
Claims
Application Information

- R&D
- Intellectual Property
- Life Sciences
- Materials
- Tech Scout
- Unparalleled Data Quality
- Higher Quality Content
- 60% Fewer Hallucinations
Browse by: Latest US Patents, China's latest patents, Technical Efficacy Thesaurus, Application Domain, Technology Topic, Popular Technical Reports.
© 2025 PatSnap. All rights reserved.Legal|Privacy policy|Modern Slavery Act Transparency Statement|Sitemap|About US| Contact US: help@patsnap.com