Preparation method for reducing sulfur impurities in electrolytic nickel
A technology for electrolysis of nickel and impurities, which is applied in the direction of electrolysis process, electrolysis components, process efficiency improvement, etc., can solve the problems of impurities sulfur exceeding the standard, achieve the effect of improving sulfur content, high product quality, and improving product quality
- Summary
- Abstract
- Description
- Claims
- Application Information
AI Technical Summary
Problems solved by technology
Method used
Image
Examples
Embodiment 1
[0039] The high nickel matte is cast into the anode plate, placed in the electrolytic cell for direct electrolysis of the nickel sulfide anode, the cathode is the nickel starting plate produced by the seed plate tank, the cathode is placed in the diaphragm bag, and the purified electrolyte enters the cathode chamber, the cathode chamber The liquid level is always higher than that of the anode chamber, so that the anolyte with high impurities cannot enter the cathode chamber. Electrolytic nickel is produced by passing electricity in the electrolytic cell. The purification of anolyte adopts three stages of purification: copper removal by extraction, iron removal by oxidation neutralization and cobalt removal by extraction. After normal electrolysis, the impurity sulfur content in the produced electrolytic nickel is as high as 0.1% to 0.005%, and the impurity sulfur content is too high, which seriously affects the electrolysis process. Nickel quality.
Embodiment 2
[0041] The high nickel matte is cast into the anode plate, placed in the electrolytic cell for direct electrolysis of the nickel sulfide anode, the cathode is the nickel starting plate produced by the seed plate tank, the cathode is placed in the diaphragm bag, and the purified electrolyte enters the cathode chamber, the cathode chamber The liquid level is always higher than that of the anode chamber, so that the anolyte with high impurities cannot enter the cathode chamber. Electrolytic nickel is produced by passing electricity in the electrolytic cell. Anolyte purification adopts four-stage purification of extracting copper, oxidizing and neutralizing iron, extracting cobalt and chlorine to reduce sulfur. Among them, chlorine sulfur reduction adopts 20Nm 3 / h~30Nm 3 / h corresponds to electrolyte 40m 3 / h~60m 3 / h reacts in the pipeline to reduce sulfur. After normal electrolysis, the impurity sulfur in the produced electrolytic nickel is less than 0.01%, which is difficu...
Embodiment 3
[0043] The high nickel matte is cast into the anode plate, placed in the electrolytic cell for direct electrolysis of the nickel sulfide anode, the cathode is the nickel starting plate produced by the seed plate tank, the cathode is placed in the diaphragm bag, and the purified electrolyte enters the cathode chamber, the cathode chamber The liquid level is always higher than that of the anode chamber, so that the anolyte with high impurities cannot enter the cathode chamber. Electrolytic nickel is produced by passing electricity in the electrolytic cell. Anolyte purification adopts four-stage purification of extracting copper, oxidizing and neutralizing iron, extracting cobalt and chlorine to reduce sulfur. Among them, chlorine sulfur reduction uses 30Nm 3 / h~50Nm 3 / h corresponds to electrolyte 40m 3 / h~60m 3 / h at an effective volume of 80m 3 The storage tank reacts to reduce sulfur. After normal electrolysis, the impurity sulfur in the produced electrolytic nickel is 0...
PUM
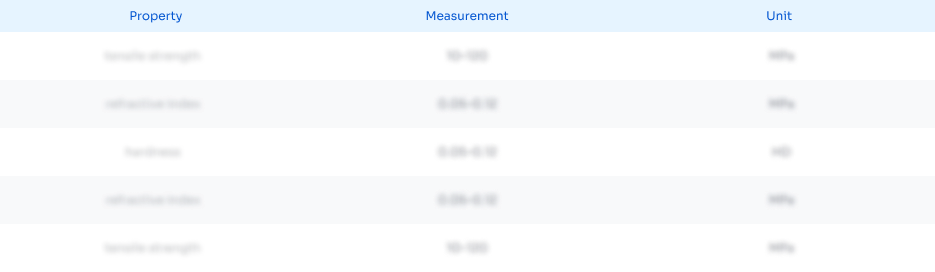
Abstract
Description
Claims
Application Information

- Generate Ideas
- Intellectual Property
- Life Sciences
- Materials
- Tech Scout
- Unparalleled Data Quality
- Higher Quality Content
- 60% Fewer Hallucinations
Browse by: Latest US Patents, China's latest patents, Technical Efficacy Thesaurus, Application Domain, Technology Topic, Popular Technical Reports.
© 2025 PatSnap. All rights reserved.Legal|Privacy policy|Modern Slavery Act Transparency Statement|Sitemap|About US| Contact US: help@patsnap.com