Method for manufacturing extra-high-voltage composite insulation paper board
A composite insulation and ultra-high voltage technology, applied in the direction of insulators, insulators, electrical components, etc., can solve problems such as low temperature resistance, poor mechanical strength, affecting the miniaturization of power transmission and transformation equipment, and the prospect of large-capacity UHV development. Achieve the effect of reducing partial discharge and lowering the dielectric constant
- Summary
- Abstract
- Description
- Claims
- Application Information
AI Technical Summary
Problems solved by technology
Method used
Image
Examples
Embodiment 1
[0030] A preparation method of UHV composite insulating paperboard, comprising the steps of:
[0031] 1) Graft modification step of aramid pulp
[0032] a) Put the aramid pulp in a Soxhlet extractor and extract it with ethanol for 10 hours, then extract it with distilled water for 10 hours, then place the aramid pulp in a vacuum environment and dry it at 100°C for 2.5 hours;
[0033] b) Under nitrogen protection, add 140ml of dimethyl sulfoxide and 0.5g of sodium hydride into a three-necked flask, and stir at 28°C for 28min. Then raise the temperature to 70° C. and stir for 38 minutes, and after cooling to 28° C., add 0.024 mol of the aramid pulp treated in step a) into the three-necked flask, and stir for 8 minutes;
[0034]c) Under the protection of nitrogen, filter the aramid pulp treated in step 2 from the three-necked flask, and transfer it to another three-necked flask containing 0.00025mol of grafted monomer and 140ml of dimethyl sulfoxide, at 28°C Under the condition...
Embodiment 2
[0043] A preparation method of UHV composite insulating paperboard, comprising the steps of:
[0044] 1) Graft modification step of aramid pulp
[0045] a) Put the aramid pulp in a Soxhlet extractor and extract it with ethanol for 11 hours, then extract it with distilled water for 11 hours, then place the aramid pulp in a vacuum environment and dry it at 110°C for 3 hours;
[0046] b) Under nitrogen protection, add 150ml of dimethyl sulfoxide and 0.6g of sodium hydride into a three-necked flask, and stir at 30°C for 30min. Then raise the temperature to 72°C and stir for 40 minutes, and after cooling to 30°C, add 0.025 mol of the aramid pulp treated in step a) into the three-necked flask, and stir for 10 minutes;
[0047] c) Under nitrogen protection, filter the aramid pulp treated in step 2 from the three-necked flask, and transfer it to another three-necked flask containing 0.0005mol of grafted monomer and 150ml of dimethyl sulfoxide, at 30°C Under the condition of reaction...
Embodiment 3
[0056] A preparation method of UHV composite insulating paperboard, comprising the steps of:
[0057] 1) Graft modification step of aramid pulp
[0058] a) Put the aramid pulp in a Soxhlet extractor and extract it with ethanol for 12 hours, then extract it with distilled water for 12 hours, then place the aramid pulp in a vacuum environment and dry it at 120°C for 3.5 hours;
[0059] b) Under nitrogen protection, add 160ml of dimethyl sulfoxide and 0.7g of sodium hydride into a three-necked flask, and stir for 32min at 32°C. Then raise the temperature to 74°C and stir for 42 minutes, and after cooling to 32°C, add 0.026 mol of the aramid pulp treated in step a) into the three-necked flask, and stir for 12 minutes;
[0060] c) Under nitrogen protection, filter the aramid pulp treated in step 2 from the three-necked flask, and transfer it to another three-necked flask containing 0.00125mol of grafted monomer and 160ml of dimethyl sulfoxide, at 32°C Under the condition of react...
PUM
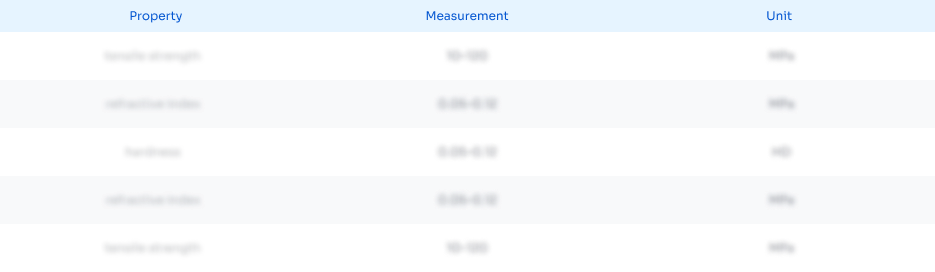
Abstract
Description
Claims
Application Information

- Generate Ideas
- Intellectual Property
- Life Sciences
- Materials
- Tech Scout
- Unparalleled Data Quality
- Higher Quality Content
- 60% Fewer Hallucinations
Browse by: Latest US Patents, China's latest patents, Technical Efficacy Thesaurus, Application Domain, Technology Topic, Popular Technical Reports.
© 2025 PatSnap. All rights reserved.Legal|Privacy policy|Modern Slavery Act Transparency Statement|Sitemap|About US| Contact US: help@patsnap.com