Platinum refining technology
A new process, the technology of ammonium chloroplatinate, applied in the field of platinum refining, can solve the problems of complex process and low production efficiency, and achieve the effects of simple process flow, low cost and reasonable connection
- Summary
- Abstract
- Description
- Claims
- Application Information
AI Technical Summary
Problems solved by technology
Method used
Image
Examples
Embodiment 1
[0016] Add 800ml of deionized water and 100g of platinum-group metal-containing materials containing ammonium chloroplatinate into a 2L beaker to form a slurry, and add 150ml of 12mol / L analytically pure hydrochloric acid to the slurry under constant stirring to adjust the slurry The acidity is 1.8mol / L, and then heated on an electric heating plate. After the slurry is heated to a boiling state, 27g of reducing agent ammonium oxalate is added. After one hour of reaction, 5g is added, and then 4g is added every half hour, twice in total. , that is, add 40 g of reducing agent ammonium oxalate in 2 hours of reaction, and then react for half an hour to completely dissolve the ammonium chloroplatinate. Filter the dissolved solution, add 150g of ammonium chloride solid to the filtrate, stir and dissolve, and after heating up to 85°C, pass chlorine gas into the fume hood for 10 minutes. The flow rate of chlorine gas is 25L / h. Ammonium platinum is re-precipitated. After the chlorine ...
Embodiment 2
[0019] Add 1000ml of pure water and 100g of platinum-group metal-containing material containing ammonium chloroplatinate into a 2L beaker to form a slurry, and add 150ml of 12mol / L analytically pure hydrochloric acid under constant stirring to adjust the acidity of the slurry to 2.0mol / L L, then transferred to the reaction kettle, heated to boiling state, added 33g of reducing agent ammonium oxalate in the state of boiling, added 5g after one hour of reaction, and then added 4g every half hour, a total of 3 times, that is, in After 2 hours of reaction, 50 g of reducing agent ammonium oxalate was added, and the ammonium chloroplatinate was completely dissolved in the reaction for about half an hour. During the dissolution process, the ammonium chloroplatinate precipitate gradually disappeared and bubbles were released continuously and steadily, and the solution finally turned rose red. Filter the solution, put the filtered filtrate in a reaction kettle, then add 100g of amm...
PUM
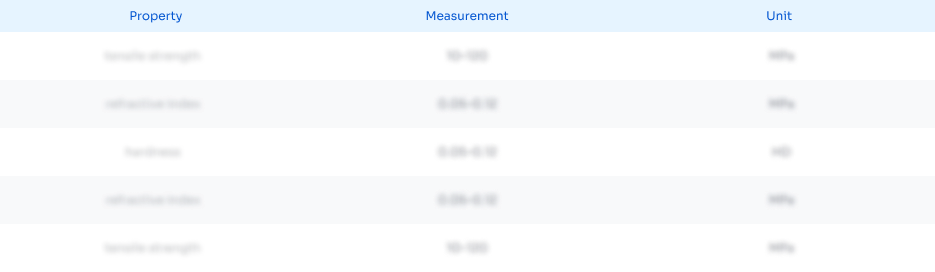
Abstract
Description
Claims
Application Information

- R&D
- Intellectual Property
- Life Sciences
- Materials
- Tech Scout
- Unparalleled Data Quality
- Higher Quality Content
- 60% Fewer Hallucinations
Browse by: Latest US Patents, China's latest patents, Technical Efficacy Thesaurus, Application Domain, Technology Topic, Popular Technical Reports.
© 2025 PatSnap. All rights reserved.Legal|Privacy policy|Modern Slavery Act Transparency Statement|Sitemap|About US| Contact US: help@patsnap.com