Matrix resin for carbon fiber composite material and preparation method of matrix resin
A matrix resin and composite material technology, applied in the field of matrix resin for carbon fiber composite materials and its preparation, can solve the problems of high cost of polyetherimide resin, unfavorable large-scale popularization and application, and small linear expansion coefficient, etc., to achieve a good comprehensive The effect of high performance, low cost and convenient operation
- Summary
- Abstract
- Description
- Claims
- Application Information
AI Technical Summary
Problems solved by technology
Method used
Image
Examples
Embodiment 1
[0039] Mix 1000 g of N,N,N',N'-tetraglycidyl-4,4'-diaminodiphenyl ether (TGDADPE) epoxy resin with 50 g of 3,3'-dimethyl-4,4'- Put bis(4-carboxyphthalimido)diphenylmethane into the reaction kettle, stir and react at 80°C for 0.5 hours, add 500 grams of ES216 epoxy resin and 500 grams of 2,2-bis[4-(2- Trifluoromethyl-4-maleimidophenoxy)phenyl]propane, continue to stir for 0.5 hours, add 500 grams of toluene and 300 grams of acetone, stir well to obtain 2850 grams of component A, denoted as A1 .
[0040] 300 grams of phthalic anhydride, 200 grams of 2,2-bis(3,4-dicarboxyphenoxy)hexafluoropropane dianhydride and 25 grams of 1,8-diazabicyclo(5.4.0)undec-7-ene , 2000 grams of N-methyl-2-pyrrolidone and 200 grams of tetrahydrofuran were mixed, stirred and dissolved in a homogeneous phase to obtain 2725 grams of component B, which was denoted as B1.
[0041] When in use, mix 2850 grams of component A1 and 2725 grams of component B1 evenly to obtain 5575 grams of matrix resin for ca...
Embodiment 2
[0043] Mix 1000 g of N,N,N',N'-tetraglycidyl-4,4'-diaminodiphenyl ether (TGDADPE) epoxy resin and 200 g of 3,3'-dimethyl-4,4'- Put bis(4-carboxyphthalimido)diphenylmethane into the reaction kettle, stir and react at 100°C for 1 hour, add 1000 grams of ES216 epoxy resin and 100 grams of 2,2-bis[4-(2- Trifluoromethyl-4-maleimidophenoxy)phenyl]propane, continue to stir and react for 1 hour, add 600 grams of xylene and 400 grams of acetone, stir well to get 3300 grams of A component, denoted as A2.
[0044] 100 grams of 3,3',4,4'-tetracarboxydiphenyl ether dianhydride, 400 grams of 2,2-bis(3,4-dicarboxyphenoxy)propane dianhydride, 200 grams of 2,2-bis (3,4-Dicarboxyphenoxy)hexafluoropropane dianhydride and 140 grams of 1,8-diazabicyclo(5.4.0)undec-7-ene, 4000 grams of N-methyl-2-pyrrolidone and Mix 1000 grams of methyl tetrahydrofuran, stir and dissolve to form a homogeneous phase, and obtain 5840 grams of component B, which is recorded as B2.
[0045] When in use, mix 3300 gra...
Embodiment 3
[0047] Take an appropriate amount of matrix resins for carbon fiber composite materials of A1B1 and A2B2 in the above-mentioned examples 1 and 2, and apply them evenly on the standard stainless steel test pieces respectively. After airing at room temperature for 1 hour, stack them, clamp them tightly, and put them into the air blast. Curing in an oven: heat from room temperature to 60°C, hold for 1 hour, continue to heat up to 110°C, hold for 3 hours, continue to heat up to 140°C, hold for 3 hours, continue to heat up to 180°C, hold for 2 hours, and naturally cool to room temperature . The measured tensile shear strengths are shown in Table 1.
[0048] Take an appropriate amount of matrix resin for carbon fiber composite materials of A1B1 and A2B2 in the above-mentioned Examples 1 and 2, and pour it into a stainless steel disc with a diameter of 10 cm (the disc is coated with a release agent in advance), heat curing: heating from room temperature to 60°C, hold for 1 hour, con...
PUM
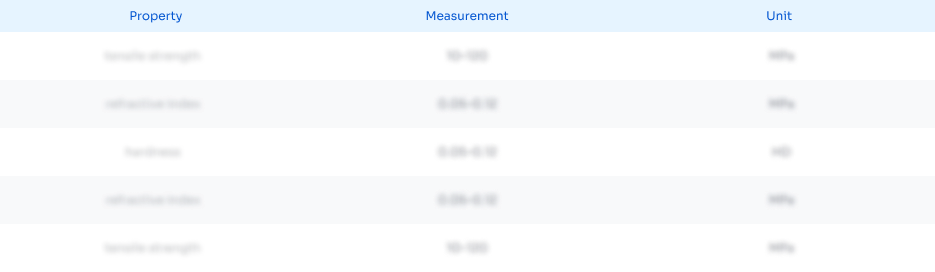
Abstract
Description
Claims
Application Information

- R&D
- Intellectual Property
- Life Sciences
- Materials
- Tech Scout
- Unparalleled Data Quality
- Higher Quality Content
- 60% Fewer Hallucinations
Browse by: Latest US Patents, China's latest patents, Technical Efficacy Thesaurus, Application Domain, Technology Topic, Popular Technical Reports.
© 2025 PatSnap. All rights reserved.Legal|Privacy policy|Modern Slavery Act Transparency Statement|Sitemap|About US| Contact US: help@patsnap.com