A method for producing synthetic ammonia from furnace gas produced by kiln method or blast furnace method to produce phosphoric acid
A blast furnace method and a technology for synthesizing ammonia, which are applied in the fields of comprehensive utilization of resources and ammonia synthesis, can solve problems such as direct exhaust emission, air pollution, environmental impact, etc., and achieve the effects of high raw material utilization, environmental friendliness, good social and economic benefits
- Summary
- Abstract
- Description
- Claims
- Application Information
AI Technical Summary
Problems solved by technology
Method used
Image
Examples
Embodiment 1
[0030] Raw materials: Blast furnace gas for phosphoric acid production by blast furnace method.
[0031] A method for producing synthetic ammonia from furnace gas produced by a kiln method or a blast furnace method to produce phosphoric acid, comprising the steps of:
[0032] (1) The blast furnace gas produced by blast furnace process phosphoric acid is firstly cooled in a water bath at room temperature to remove phosphorus vapor and most of the dust in the phosphorus receiving tank, and then the exhaust gas is obtained by venturi tube and fiber demister successively. The main components of the exhaust gas are as follows: The volume percentage is shown in the table below:
[0033]
[0034] (2) The tail gas is desulfurized by wet oxidation first; after the above-mentioned desulfurization, it enters the conversion process. The conversion process is that the carbon monoxide in the tail gas reacts with water in the presence of catalyst HT-CB5 / 9 to produce hydrogen, and the obta...
Embodiment 2
[0037] Raw materials: Blast furnace gas for phosphoric acid production by blast furnace method.
[0038] A method for producing synthetic ammonia from furnace gas produced by a kiln method or a blast furnace method to produce phosphoric acid, comprising the steps of:
[0039] (1) The blast furnace gas produced by blast furnace process phosphoric acid is firstly rinsed and cooled by 3-stage absorption towers connected in series with normal temperature water to remove phosphorus vapor and most of the dust, and then dedusted by venturi tube and fiber demister successively to obtain tail gas. The main components of exhaust gas are shown in the following table by volume percentage:
[0040]
[0041] (2) The tail gas is desulfurized by wet oxidation first; after the above desulfurization, it enters the conversion process. The conversion process is that carbon monoxide in the tail gas reacts with water in the presence of BS113-2 catalyst to produce hydrogen, and the obtained hydro...
Embodiment 3
[0044] Raw materials: Blast furnace gas for phosphoric acid production by blast furnace method.
[0045] A method for producing synthetic ammonia from furnace gas produced by a kiln method or a blast furnace method to produce phosphoric acid, comprising the steps of:
[0046] (1) The blast furnace gas produced by blast furnace process phosphoric acid is firstly cooled in a water bath at room temperature to remove phosphorus vapor and most of the dust in the phosphorus receiving tank, and then the exhaust gas is obtained by venturi tube and fiber demister successively. The main components of the exhaust gas are as follows: The volume percentage is shown in the table below:
[0047]
[0048] (2) The tail gas is desulfurized by wet oxidation first; after the desulfurization above, it enters the transformation process. The transformation process is that the carbon monoxide in the tail gas reacts with water in the presence of catalyst HT-B113 to produce hydrogen, and the obtaine...
PUM
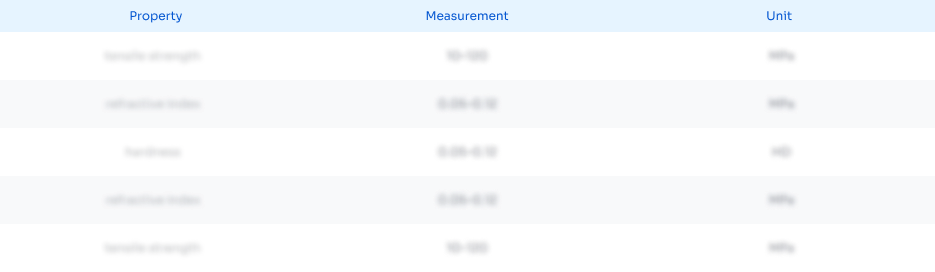
Abstract
Description
Claims
Application Information

- R&D Engineer
- R&D Manager
- IP Professional
- Industry Leading Data Capabilities
- Powerful AI technology
- Patent DNA Extraction
Browse by: Latest US Patents, China's latest patents, Technical Efficacy Thesaurus, Application Domain, Technology Topic, Popular Technical Reports.
© 2024 PatSnap. All rights reserved.Legal|Privacy policy|Modern Slavery Act Transparency Statement|Sitemap|About US| Contact US: help@patsnap.com