Preparation method of high-purity yttrium oxide
A high-purity, yttrium oxide technology, applied in chemical instruments and methods, inorganic chemistry, rare earth metal compounds, etc., can solve the problems of waste of resources, low purity, damage to the environment, etc., to save acid and alkali consumption, and save rare earth Effects of conservation of resources and recycling
- Summary
- Abstract
- Description
- Claims
- Application Information
AI Technical Summary
Problems solved by technology
Method used
Examples
Embodiment 1
[0028]A) Pretreatment, the rare earth chloride solution containing Ho, Er, Tm, Yb, Lu and Y enrichment and tertiary amine, which is customarily called N235, tri(octyl-decyl)alkyl tertiary amine, in a volume ratio of 1 : 3 drop into a container with a stirring device and stir for 60min at a speed of 150rpm at the rotating speed of the stirring device to obtain a pretreated rare earth chloride solution, wherein: the rare earth chloride solution is preferably purchased from a commercial channel, such as Purchase and use the trade mark that is produced and sold by China Inner Mongolia Baotou Pioneer Rare Earth Co., Ltd. to be XFA-D-2 rare earth chloride solution, and the mass percent content of yttrium in this rare earth chloride solution is 70%, and the mass percent concentration of hydrochloric acid 0.007%;
[0029] B) Pre-balance, put the first extractant and the pre-treated rare earth chloride solution obtained in step A) into a container with a stirring device, and add the al...
Embodiment 2
[0036] Only change the volume ratio of the rare earth chloride solution in step A) to the tri(octyl-decyl)alkyl tertiary amine to 1:1, change the rotating speed of the stirring device, that is, the stirring speed to 80rpm, and the stirring time to 120min, Change the mass percentage of yttrium in the rare earth chloride solution to 60%, change the mass percentage concentration of hydrochloric acid to 0.01%; change the pH value in step B) to 5, and change the pretreated rare earth chloride solution, The volume ratio of the first extraction agent and the alkaline regulator is changed to 1: 1: 0.15, the mass percentage concentration of the alkaline regulator is changed to 32%, the time and the rotating speed of the continuous stirring are changed to 120min and 80rpm respectively, The dropping time of liquid caustic soda is changed into 120min, and the volume ratio of naphthenic acid, additive and diluent is changed into 1:1:2.5; The molar concentration of the yttrium-rich material ...
Embodiment 3
[0038] Only change the volume ratio of the rare earth chloride solution in step A) to the tri(octyl-decyl)alkyl tertiary amine to 1:2, change the rotating speed of the stirring device, that is, the stirring speed to 115rpm, and change the stirring time to 90min. Change the mass percentage of yttrium in the rare earth chloride solution to 70%, change the mass percentage concentration of hydrochloric acid to 0.085%; change the pH value in step B) to 4.5, and change the pretreated rare earth chloride solution, The volume ratio of the first extraction agent and the basic conditioner is changed to 1: 2: 0.1, the mass percentage concentration of the basic conditioner is changed to 31%, the time and the rotating speed of the continuous stirring are changed to 90min and 125rpm respectively, The dropping time of liquid caustic soda is changed into 90min, and the volume ratio of naphthenic acid, additive and diluent is changed into 1: 0.85: 2.65; The molar concentration of the yttrium-ri...
PUM
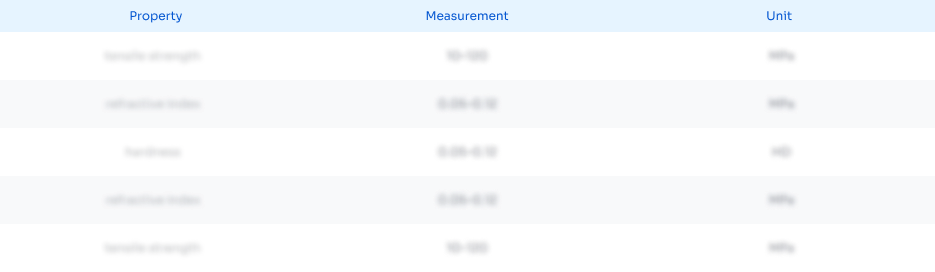
Abstract
Description
Claims
Application Information

- R&D
- Intellectual Property
- Life Sciences
- Materials
- Tech Scout
- Unparalleled Data Quality
- Higher Quality Content
- 60% Fewer Hallucinations
Browse by: Latest US Patents, China's latest patents, Technical Efficacy Thesaurus, Application Domain, Technology Topic, Popular Technical Reports.
© 2025 PatSnap. All rights reserved.Legal|Privacy policy|Modern Slavery Act Transparency Statement|Sitemap|About US| Contact US: help@patsnap.com