Method for recycling exhausted exchange resin during recovering process of silicon wafer wire cutting liquid
A technology of ion exchange resin and wire cutting, applied in the directions of ion exchange regeneration, ion exchange, ion exchange bed cleaning/flushing, etc., can solve problems such as cumbersome operation steps, environmental pollution, and influence of silicon wafer cutting, and achieve reasonable temperature control, The method is easy to operate and the effect of short contact time
- Summary
- Abstract
- Description
- Claims
- Application Information
AI Technical Summary
Problems solved by technology
Method used
Examples
Embodiment 1
[0040] Recovery of 001×7 gel-type strong acid styrene-based cation resin:
[0041] 1) Put 001×7 gel-type strong acid styrene cationic resin into the recovery tank in batches, add water and stir to remove the broken resin, and then drain the water in the recovery tank;
[0042] 2) After the water is drained, soak 001×7 gel type strong acid styrene cation resin in 5% hydrochloric acid solution, the volume of hydrochloric acid solution is 001×7 gel type strong acid styrene cation resin volume 2 times, soaking time is 8 hours, stirring once per hour, stirring time is 30min.
[0043] 3) After the treatment in step 2), drain the acid solution, rinse with water, and the water discharged from the discharge port is close to neutral. Then prepare 001×7 gel-type strong acidic styrenic cation resin resuscitation solution with 2 times the volume. The resuscitation solution contains 5% NaCl, 5% NaOH and 5% Na 3 PO 4 , and the balance is water; take half of the prepared resuscitation flui...
Embodiment 2
[0047] Recovery of 201×7 gel-type strongly basic styrene-based anion resin:
[0048] 1) Put 201×7 gel-type strongly basic styrene-based anion resin in batches into the resuscitation bucket, add water and stir to remove the broken resin, and then drain the water in the resuscitation bucket;
[0049] 2) Soak the 201×7 gel-type strongly basic styrene-based anion resin treated in step 1) in a salt solution with a mass concentration of 4%, and drain the salt solution after soaking for 30 minutes; The gel-type strongly basic styrene-based anion resin is soaked in a hydrochloric acid solution with a mass concentration of 10%. The volume of the hydrochloric acid solution is twice that of the 201×7 gel-type strong-basic styrene-based anion resin, and the soaking time is 8 hours. , stirring once an hour, stirring time 30min.
[0050] 3) After the treatment in step 2), drain the acid solution, rinse with water, and the water discharged from the discharge port is close to neutral. Then ...
Embodiment 3
[0056] Recovery of 001×7 gel-type strong acid styrene-based cation resin:
[0057] 1) Put 001×7 gel-type strong acid styrene cationic resin into the recovery tank in batches, add water and stir to remove the broken resin, and then drain the water in the recovery tank;
[0058] 2) After the water is drained, soak 001×7 gel type strong acid styrene cation resin in 10% hydrochloric acid solution, the volume of hydrochloric acid solution is 001×7 gel type strong acid styrene cation resin volume 2 times, soaking time is 4 hours, stirring once per hour, stirring time is 30min.
[0059] 3) After the treatment in step 2), drain the acid solution, rinse with water, and the water discharged from the discharge port is close to neutral. Then prepare a resuscitation solution with 4 times the volume of 001×7 gel-type strong acid styrene-based cation resin, which contains 10% NaCl, 6% NaOH and 3% Na 3 PO 4 , and the balance is water; take half of the prepared resuscitation fluid and wash ...
PUM
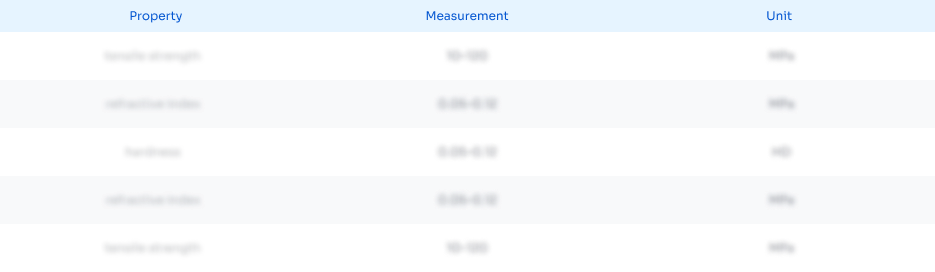
Abstract
Description
Claims
Application Information

- R&D Engineer
- R&D Manager
- IP Professional
- Industry Leading Data Capabilities
- Powerful AI technology
- Patent DNA Extraction
Browse by: Latest US Patents, China's latest patents, Technical Efficacy Thesaurus, Application Domain, Technology Topic, Popular Technical Reports.
© 2024 PatSnap. All rights reserved.Legal|Privacy policy|Modern Slavery Act Transparency Statement|Sitemap|About US| Contact US: help@patsnap.com