Method for predicting residual life of corroded casing of high-temperature and high-pressure well
A high temperature and high pressure, casing technology, applied in special data processing applications, instruments, electrical digital data processing and other directions, can solve the problems of corrosion, well scrapping, complex and changeable underground service environment, etc., to extend service life and ensure accuracy. , Easy to adjust the effect of downhole process parameters
- Summary
- Abstract
- Description
- Claims
- Application Information
AI Technical Summary
Problems solved by technology
Method used
Image
Examples
Embodiment Construction
[0031] The present invention will be further described and elaborated below in conjunction with the accompanying drawings.
[0032] Since corrosion seriously affects the service life of the bushing, there is no special formula for calculating the remaining life of the bushing in theory. Considering the insufficiency of laboratory tests and field data in predicting the remaining life of the bushing, the present invention proposes the use of gray neural network for the first time. The network algorithm is used to predict the corrosion rate of the casing, and the finite element model and element life-and-death technology are used to accurately simulate the corrosion failure process of the casing, and then according to the established model of the remaining life of the corroded casing, the service life of the high-temperature and high-pressure well is predicted. remaining life.
[0033] In the process of predicting the remaining life of corroded casing, the gray neural network alg...
PUM
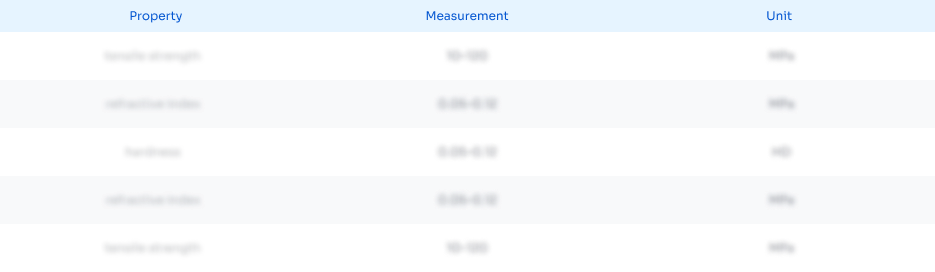
Abstract
Description
Claims
Application Information

- R&D
- Intellectual Property
- Life Sciences
- Materials
- Tech Scout
- Unparalleled Data Quality
- Higher Quality Content
- 60% Fewer Hallucinations
Browse by: Latest US Patents, China's latest patents, Technical Efficacy Thesaurus, Application Domain, Technology Topic, Popular Technical Reports.
© 2025 PatSnap. All rights reserved.Legal|Privacy policy|Modern Slavery Act Transparency Statement|Sitemap|About US| Contact US: help@patsnap.com