Coal natural gas methanation technology and system thereof
A coal-to-natural gas and methanation technology, which is applied in the field of methanation process and its system, can solve the problems of high outlet temperature of the main methanation reactor, influence the service life of equipment, damage catalysts and equipment, etc., and achieves increased control means and adjustment Method, avoid metal dusting reaction, prevent contact effect
- Summary
- Abstract
- Description
- Claims
- Application Information
AI Technical Summary
Problems solved by technology
Method used
Image
Examples
Embodiment Construction
[0032] The system of the present invention will be further explained below in conjunction with the accompanying drawings:
[0033] The ejector U01 passes through the pipeline in turn through the purified gas preheater E01, 1# separator S01, four methane reactors, namely 1# methane reactor R01, 2# methane reactor R02, 3# methane reactor R03, 4# methane Reactor R04, 2# boiler feed water preheating E06, and 2# separator S02 are sequentially connected in series; among the four methane reactors connected in series, the synthesis gas outlet of 1# methane reactor R01 passes through 1# waste pot E02 and The connection of the synthesis gas inlet of 2# methane reactor R02, the synthesis gas outlet of 2# methane reactor R02 is connected with the synthesis gas inlet of 3# methane reactor R03 through 2# waste pot E03, steam superheater E04, the 3 The synthesis gas outlet of #methane reactor R03 is connected to the synthesis gas inlet of 4# methane reactor R03 through purifier preheater E01...
PUM
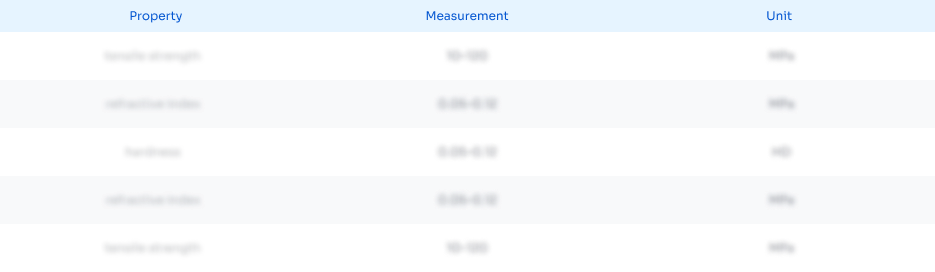
Abstract
Description
Claims
Application Information

- R&D Engineer
- R&D Manager
- IP Professional
- Industry Leading Data Capabilities
- Powerful AI technology
- Patent DNA Extraction
Browse by: Latest US Patents, China's latest patents, Technical Efficacy Thesaurus, Application Domain, Technology Topic, Popular Technical Reports.
© 2024 PatSnap. All rights reserved.Legal|Privacy policy|Modern Slavery Act Transparency Statement|Sitemap|About US| Contact US: help@patsnap.com