Banking method for damping down of large blast furnace
A blast furnace and large-scale technology, which is applied in the field of furnace closure of large-scale blast furnaces, can solve the problems of unreasonable metallurgical properties of raw materials, affecting furnace opening, and difficulty in opening furnace, and achieve stable furnace conditions, improve production efficiency, and improve the fluidity of iron slag. Good results
- Summary
- Abstract
- Description
- Claims
- Application Information
AI Technical Summary
Problems solved by technology
Method used
Examples
Embodiment 1
[0023] 3200m 3 The furnace sealing method of the 1 ton blast furnace shutdown, the steps:
[0024] 1) 45 hours before the blast furnace shut down, add manganese ore into the blast furnace, the amount of addition is to make the Mn weight percentage content in the molten iron 0.8% as a principle;
[0025] 2) 7 hours before the wind break, add material to the furnace in the following way:
[0026] A. First load coke to the upper edge of the hearth, that is, the hearth is completely filled with coke;
[0027] B. Add the following materials and amounts into the bosh until the bosh is full: according to the effective volume of the blast furnace 10 kg / m 3 Add manganese ore, according to the blast furnace effective volume 5kg / m 3 Add limestone, according to the blast furnace effective volume 3 kg / m 3 Add serpentine, and all the rest is coke;
[0028] C. Load all the empty materials in batches in the furnace waist, and the amount of materials added in each batch is: according to ...
Embodiment 2
[0036] The furnace sealing method of 3200 ton blast furnace shutdown, its steps:
[0037] 1) 50 hours before the blast furnace shut down, add manganese ore into the blast furnace, the amount of addition is in principle to make the Mn weight percentage content in the molten iron 0.85%;
[0038] 2) 6.5 hours before the wind break, add material to the furnace in the following way:
[0039] A. First load coke to the upper edge of the hearth, that is, the hearth is completely filled with coke;
[0040] B. Add the following materials and amounts into the bosh until the bosh is full: according to the effective volume of the blast furnace 11 kg / m 3 Add manganese ore, according to the blast furnace effective volume 5.5kg / m 3 Add limestone, according to the blast furnace effective volume 3 kg / m 3 Add serpentine, and all the rest is coke;
[0041] C. Fill all empty materials in batches in the furnace waist, and the amount and amount of materials added in each batch are: according to...
Embodiment 3
[0049] The furnace sealing method of 2200 ton blast furnace shutdown, its steps:
[0050] 1) 50 hours before the blast furnace shut down, add manganese ore into the blast furnace, the amount of addition is to make the Mn weight percentage content in the molten iron 0.9% as a principle;
[0051] 2) 7 hours before the wind break, add material to the furnace in the following way:
[0052] A. First load coke to the upper edge of the hearth, that is, the hearth is completely filled with coke;
[0053] B. Add the following materials and amounts into the bosh until the bosh is full: according to the blast furnace effective volume of 10.5 kg / m 3 Add manganese ore, according to the blast furnace effective volume 5.3kg / m 3 Add limestone, according to the blast furnace effective volume 3 kg / m 3 Add serpentine, and all the rest is coke;
[0054] C. Fill all the empty materials in batches in the furnace waist, and the amount of materials added in each batch is: according to the effect...
PUM
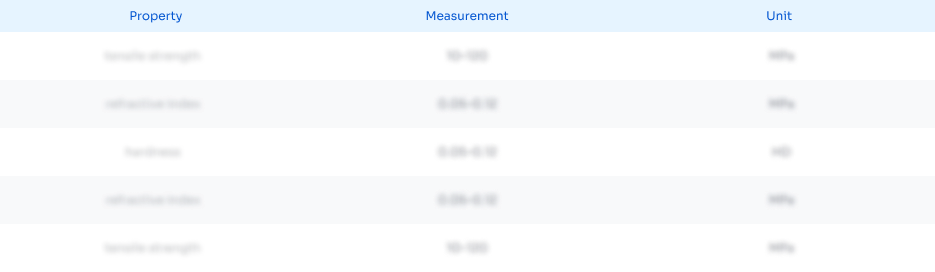
Abstract
Description
Claims
Application Information

- R&D Engineer
- R&D Manager
- IP Professional
- Industry Leading Data Capabilities
- Powerful AI technology
- Patent DNA Extraction
Browse by: Latest US Patents, China's latest patents, Technical Efficacy Thesaurus, Application Domain, Technology Topic, Popular Technical Reports.
© 2024 PatSnap. All rights reserved.Legal|Privacy policy|Modern Slavery Act Transparency Statement|Sitemap|About US| Contact US: help@patsnap.com