Composite material chimney connection joint and method
A technology of composite materials and connecting nodes, which is applied in the direction of combustion methods, combustion product treatment, exhaust gas devices, etc., can solve the problems of heavy field work workload, cracking and damage of flanges, poor ability to eliminate stress, etc., and achieve reduction of direct Contact area, reduce anti-corrosion cost, improve the overall effect
- Summary
- Abstract
- Description
- Claims
- Application Information
AI Technical Summary
Problems solved by technology
Method used
Image
Examples
Embodiment 1
[0055] see figure 1 , figure 2 , image 3 , Figure 4 , Figure 5 , Figure 6 , Figure 7 , Figure 8 and Figure 9 Shown:
[0056] First, use a grinder to grind off the non-slip coating in the node connection area of the first cylinder 11 and the second cylinder 12 of the composite material chimney. When grinding, care should be taken to control the grinding depth, preferably 0.5mm±0.1mm;
[0057] Next, calibrate the size of the nodes on the first cylinder 11 and the second cylinder 12, and apply epoxy glue on the node connection between the first cylinder 11 and the second cylinder 12, with a thickness of 0.5mm±0.1mm appropriate;
[0058] Next, place the first arc-shaped stabbing plate 21 on the outer surface of the node connection area of the first cylinder 11, the first connecting portion 211 is close to the connecting end of the first cylinder 11, and the barbed spine of the first arc-shaped stabbing plate 21 Facing the first cylinder body 11, press the tho...
PUM
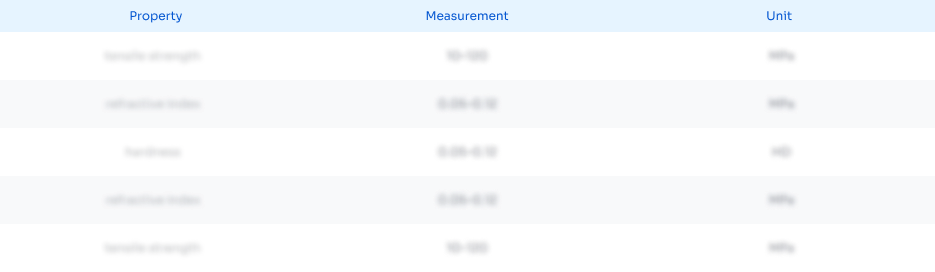
Abstract
Description
Claims
Application Information

- Generate Ideas
- Intellectual Property
- Life Sciences
- Materials
- Tech Scout
- Unparalleled Data Quality
- Higher Quality Content
- 60% Fewer Hallucinations
Browse by: Latest US Patents, China's latest patents, Technical Efficacy Thesaurus, Application Domain, Technology Topic, Popular Technical Reports.
© 2025 PatSnap. All rights reserved.Legal|Privacy policy|Modern Slavery Act Transparency Statement|Sitemap|About US| Contact US: help@patsnap.com