Technology for welding carbon steel overlaying welding layer of tube plate of high pressure heat exchanger with low carbon steel tube in sealing way
A technology of surfacing, low carbon steel, applied in manufacturing tools, welding equipment, arc welding equipment, etc., can solve the problems of high water supply pressure, large water supply resistance of sealing welding structure, sealing welding leakage, etc., and achieve smooth surface of the weld. smooth effect
- Summary
- Abstract
- Description
- Claims
- Application Information
AI Technical Summary
Problems solved by technology
Method used
Examples
Embodiment 1
[0025] A high-pressure heat exchanger tube sheet carbon steel surfacing layer and low-carbon steel pipe sealing welding process, the process is as follows:
[0026] Submerged arc surfacing welding of carbon steel on the tube sheet of the high-pressure heat exchanger. After passing the UT and MT flaw detection, the surfacing layer and the tube sheet are heat treated, and the surfacing layer is machined to 6.0mm. The tube sheet groove structure: tube sheet stack The bevel chamfer of the welding layer sealing welding is 2×45 degrees, using a flush groove pattern, the low-carbon steel pipe is flush with the tube plate surfacing layer, and the low-carbon steel pipe extending out of the tube plate surfacing layer is controlled at 0-0.5 mm, and clean the inside of the tube plate hole, the sealing welding groove and the end of the low carbon steel pipe, free of water, rust and oil.
[0027] The welded joint has a smooth transition with the tube sheet surfacing layer, and the connection wit...
PUM
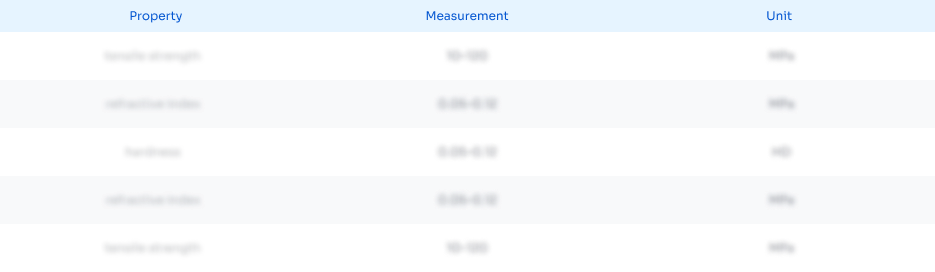
Abstract
Description
Claims
Application Information

- R&D
- Intellectual Property
- Life Sciences
- Materials
- Tech Scout
- Unparalleled Data Quality
- Higher Quality Content
- 60% Fewer Hallucinations
Browse by: Latest US Patents, China's latest patents, Technical Efficacy Thesaurus, Application Domain, Technology Topic, Popular Technical Reports.
© 2025 PatSnap. All rights reserved.Legal|Privacy policy|Modern Slavery Act Transparency Statement|Sitemap|About US| Contact US: help@patsnap.com