Production process of storage battery
A production process and battery technology, applied in lead-acid battery, lead-acid battery construction, battery pack components, etc., can solve the problems of short battery life and low liquid absorption capacity of separators
- Summary
- Abstract
- Description
- Claims
- Application Information
AI Technical Summary
Problems solved by technology
Method used
Examples
Embodiment 1
[0029] Lead powder manufacturing process:
[0030] After the electrolytic lead is crushed, it is placed in a pulverizer to make lead powder, and then the lead powder is oxidized. After the lead powder is oxidized, it is placed in the powder storage bin for 2.5 days of aging treatment before use.
[0031] Partition manufacturing process:
[0032] Mix glass fiber, expandable microcapsule polyacrylonitrile resin, and cationic polyacrylamide according to the mass ratio of 88:11:1, add water to make a colloid solution, and then dry the colloid solution to make a separator. The average glass fiber used The diameter is 1.1um.
[0033] Grid casting process:
[0034] a1: Weigh the lead, aluminum and aluminum-calcium alloy according to the mass ratio of 99.35:0.5:0.15 and put them into the melting furnace for melting at 680°C, wherein the mass ratio of aluminum and calcium elements in the aluminum-calcium alloy is 1:1.5, After smelting, add slag cleaning agent to remove scum while st...
Embodiment 2
[0046] Lead powder manufacturing process:
[0047] After the electrolytic lead is crushed, it is placed in a pulverizer to make lead powder, and then the lead powder is oxidized. After the lead powder is oxidized, it is placed in a powder storage bin and left to stand for aging treatment for 2 days before use.
[0048] Partition manufacturing process:
[0049] Mix glass fiber, expandable microcapsule polyacrylonitrile resin, and cationic polyacrylamide according to the mass ratio of 85:14:1, add water to make a colloid solution, and then dry the colloid solution to make a separator. The average glass fiber used The diameter is 1.0um.
[0050] Grid casting process:
[0051] a1: Weigh the lead, aluminum and aluminum-calcium alloy according to the mass ratio of 99.35:0.5:0.15 and put them into the melting furnace for melting at 680°C, wherein the mass ratio of aluminum and calcium elements in the aluminum-calcium alloy is 1:1.5, After smelting, add slag cleaning agent to remov...
Embodiment 3
[0063] Lead powder manufacturing process:
[0064] After the electrolytic lead is crushed, it is placed in a pulverizer to make lead powder, and then the lead powder is oxidized. After the lead powder is oxidized, it is placed in a powder storage bin and left to stand for aging treatment for 3 days before use.
[0065] Partition manufacturing process:
[0066] Mix glass fiber, expandable microcapsule polyacrylonitrile resin, and cationic polyacrylamide according to the mass ratio of 90:9:1, add water to make a colloid solution, and then dry the colloid solution to make a separator. The average glass fiber used The diameter is 1.2um.
[0067] Grid casting process:
[0068] a1: Weigh lead, aluminum and aluminum-calcium alloy according to the mass ratio of 99.35:0.5:0.15 and put them into the melting furnace for melting at 680°C, wherein the mass ratio of aluminum and calcium elements in the aluminum-calcium alloy is 1:1.5, After smelting, add slag cleaning agent to remove scu...
PUM
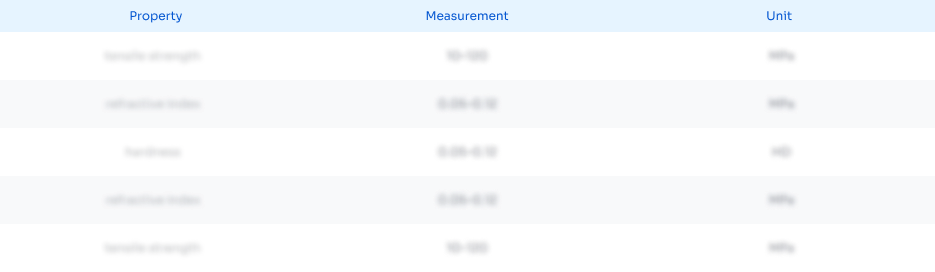
Abstract
Description
Claims
Application Information

- Generate Ideas
- Intellectual Property
- Life Sciences
- Materials
- Tech Scout
- Unparalleled Data Quality
- Higher Quality Content
- 60% Fewer Hallucinations
Browse by: Latest US Patents, China's latest patents, Technical Efficacy Thesaurus, Application Domain, Technology Topic, Popular Technical Reports.
© 2025 PatSnap. All rights reserved.Legal|Privacy policy|Modern Slavery Act Transparency Statement|Sitemap|About US| Contact US: help@patsnap.com