Preparation method of polyvinylidene fluoride-polyvinyl alcohol composite proton exchange membrane
A polyvinylidene fluoride and proton exchange membrane technology, which is applied in the field of polyvinylidene fluoride-polyvinyl alcohol composite proton exchange membrane preparation, can solve the difficulties in the synthesis of perfluorinated substances, sulfonation and film formation, high temperature and water content requirements, Reduce membrane swelling rate and other problems, achieve the effects of reduced swelling degree, good alcohol resistance performance, and low alcohol permeability
- Summary
- Abstract
- Description
- Claims
- Application Information
AI Technical Summary
Problems solved by technology
Method used
Image
Examples
Embodiment 1
[0029] Dissolve 20g of polyvinyl alcohol in a mixture of 180g of dimethyl sulfoxide and 18g of water, heat to 90°C, and stir at this temperature for 2 hours; when the temperature drops to 70°C, add 3.23g of silicon tetrachloride, 3.23g sodium tungstate and 0.6g oxalic acid, stirred at this temperature for 3 hours; heated to 120°C in a vacuum oil bath, added 5.2g PVDF, continued to stir for 2 hours, then cooled to room temperature in vacuum, and poured the formed solution on polytetrafluoroethylene Dry it on an ethylene glass plate to form a film, the thickness of the film is controlled at 0.1-0.2 mm, and the vacuum drying temperature: 110°C, that is, the desired polyvinylidene fluoride / polyvinyl alcohol composite proton doped with silicotungstic acid and silicon dioxide can be obtained exchange membrane.
[0030] Soak the membrane in deionized water for 12 hours before use. The conductivity was measured by the two-electrode AC impedance method, and the swelling degree ( SD ...
Embodiment 2
[0034] Dissolve 20g of polyvinyl alcohol in a mixture of 180g of dimethyl sulfoxide and 18g of water, heat to 90°C, and stir at this temperature for 2 hours; when the temperature drops to 70°C, add 8.8g of silicon tetrachloride, 8.8g sodium tungstate and 1.2g oxalic acid, stirred at this temperature for 3 hours; heated to 120°C in a vacuum oil bath, added 20g PVDF, continued to stir for 2 hours, then cooled to room temperature in vacuum, and poured the formed solution on polytetrafluoroethylene Dry on a glass plate to form a film, the thickness of the film is controlled at 0.1-0.2 mm, and the vacuum drying temperature is 110°C to obtain the required polyvinylidene fluoride / polyvinyl alcohol composite proton exchange doped with silicotungstic acid and silicon dioxide membrane.
Embodiment 3
[0036] Dissolve 20g of polyvinyl alcohol in a mixture of 180g of dimethyl sulfoxide and 18g of water, heat to 90°C, and stir at this temperature for 2 hours; when the temperature drops to 70°C, add 3.45g of silicon tetrachloride, 3.45g sodium tungstate and 0.69g oxalic acid, stirred at this temperature for 3 hours; heated to 120°C in a vacuum oil bath, added 6.2g PVDF, continued to stir for 2 hours, then cooled to room temperature in vacuum, and poured the formed solution on polytetrafluoroethylene Dry it on an ethylene glass plate to form a film, the thickness of the film is controlled at 0.1-0.2 mm, and the vacuum drying temperature: 110°C, that is, the desired polyvinylidene fluoride / polyvinyl alcohol composite proton doped with silicotungstic acid and silicon dioxide can be obtained exchange membrane.
PUM
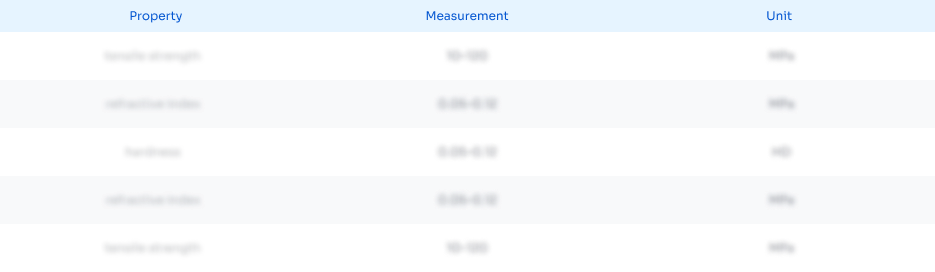
Abstract
Description
Claims
Application Information

- R&D
- Intellectual Property
- Life Sciences
- Materials
- Tech Scout
- Unparalleled Data Quality
- Higher Quality Content
- 60% Fewer Hallucinations
Browse by: Latest US Patents, China's latest patents, Technical Efficacy Thesaurus, Application Domain, Technology Topic, Popular Technical Reports.
© 2025 PatSnap. All rights reserved.Legal|Privacy policy|Modern Slavery Act Transparency Statement|Sitemap|About US| Contact US: help@patsnap.com