Printed circuit board and manufacturing method thereof
A technology for printed circuit boards and manufacturing methods, which is applied in the direction of printed circuit manufacturing, printed circuits, printed circuit components, etc., can solve the problems of high production cost, waste of raw materials, and filling rate less than 60%, so as to avoid production costs and Waste of raw materials, prevention of resin separation or breakage, and improvement of filling accuracy
- Summary
- Abstract
- Description
- Claims
- Application Information
AI Technical Summary
Problems solved by technology
Method used
Image
Examples
Embodiment 1
[0040] like figure 1 A cross-sectional view of the printed wiring board 1 is shown. The printed circuit board 1 is provided with through holes 2 . The through hole 2 extends from the upper surface 11 to the lower surface 12 of the printed circuit board. The ratio of the thickness of the printed circuit board 1 to the diameter of the through hole 2 is 10:1. Before filling, first bake the printed circuit board 1 at 100°C for 4 hours to remove moisture in the through hole 2 and make it dry.
[0041]Fill the via hole 2 with a silk-screen device. Firstly, the first epoxy resin 3 with a viscosity of 20 Pa·s / 25° C. is filled into the through hole 2 . The thickness of the printing squeegee is 2cm, the hardness is 70°, and the squeegee angle is 8°. like figure 2 As shown, the first epoxy resin 3 protrudes from the lower surface 22 of the printed wiring board 1 . However, when filling with common screen printing equipment, a groove 4 is formed between the upper surface 32 of the...
Embodiment 2
[0048] like figure 1 A cross-sectional view of the printed wiring board 1 is shown. The printed circuit board 1 is provided with through holes 2 . The through hole 2 extends from the upper surface 11 to the lower surface 12 of the printed circuit board. The ratio of the thickness of the printed circuit board 1 to the diameter of the through hole 2 is 10:1. Before filling, first bake the printed circuit board 1 at 120° C. for 2.5 hours to remove moisture in the through hole 2 and make it dry.
[0049] Fill the via hole 2 with a silk-screen device. Firstly, 6458 bisphenol F type epoxy resin 3 with a viscosity of 35 Pa·s / 25° C. is filled into the through hole 2 . The thickness of the printing squeegee is 2cm, the hardness is 70°, and the squeegee angle is 8°. like figure 2 As shown, the 6458 bisphenol F type epoxy resin 3 protrudes from the lower surface 22 of the printed wiring board 1 . However, when filled with common silk screen equipment, a groove 4 is formed between...
Embodiment 3
[0056] like figure 1 A cross-sectional view of the printed wiring board 1 is shown. The printed circuit board 1 is provided with through holes 2 . The through hole 2 extends from the upper surface 11 to the lower surface 12 of the printed circuit board. The ratio of the thickness of the printed circuit board 1 to the diameter of the through hole 2 is 10:1. Before filling, first bake the printed circuit board 1 at 110° C. for 4 hours to remove moisture in the through hole 2 and make it dry.
[0057] Fill the via hole 2 with a silk-screen device. Firstly, the first epoxy resin 3 with a viscosity of 48 Pa·s / 25° C. is filled into the through hole 2 . The thickness of the printing squeegee is 2cm, the hardness is 70°, and the squeegee angle is 8°. like figure 2 As shown, the first epoxy resin 3 protrudes from the lower surface 22 of the printed wiring board 1 . However, when filling with common screen printing equipment, a groove 4 is formed between the upper surface 32 of ...
PUM
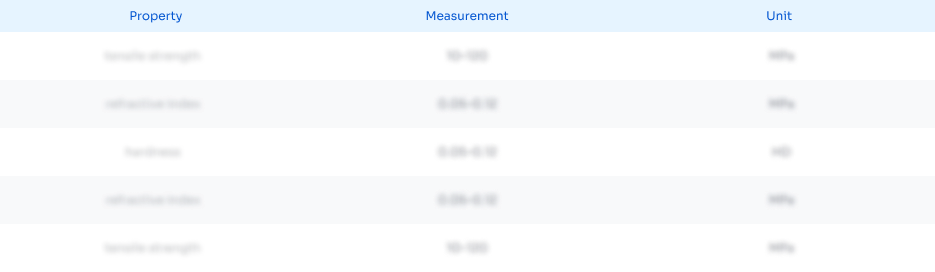
Abstract
Description
Claims
Application Information

- R&D
- Intellectual Property
- Life Sciences
- Materials
- Tech Scout
- Unparalleled Data Quality
- Higher Quality Content
- 60% Fewer Hallucinations
Browse by: Latest US Patents, China's latest patents, Technical Efficacy Thesaurus, Application Domain, Technology Topic, Popular Technical Reports.
© 2025 PatSnap. All rights reserved.Legal|Privacy policy|Modern Slavery Act Transparency Statement|Sitemap|About US| Contact US: help@patsnap.com