Back passivation solar cell and manufacturing method thereof
The technology of a solar cell and its manufacturing method, which is applied in the field of solar cells, can solve the problems that the conversion efficiency of back passivated solar cells needs to be improved, and achieve the effects of reducing carrier recombination, improving conversion efficiency, and reducing contact area
- Summary
- Abstract
- Description
- Claims
- Application Information
AI Technical Summary
Problems solved by technology
Method used
Image
Examples
Embodiment 1
[0053] This embodiment provides a method for making a back passivated solar cell, such as figure 2 As shown, the method includes:
[0054] providing a silicon wafer, the silicon wafer comprising a silicon wafer substrate, a doped layer covering the front surface of the silicon wafer substrate, and an anti-reflection layer covering the surface of the doped layer facing away from the silicon wafer substrate;
[0055] After removing the surface damage layer and preparing the textured surface of the silicon wafer, one side is diffused to form a doped layer, and the interface between the doped layer and the silicon wafer substrate forms a PN junction. Then etch the edge of the silicon wafer to remove the PN junction on the edge side of the silicon wafer, then remove the glass layer formed on the front of the silicon wafer during the diffusion process, and then PECVD (Plasma Enhanced Chemical Vapor Deposition, plasma enhanced chemical vapor deposition) on the front of the silicon w...
Embodiment 2
[0080] Based on the first embodiment, this embodiment provides a back passivated solar cell, such as Figure 5 As shown, the back passivated solar cell includes:
[0081] A silicon wafer substrate 501, a doped layer 502 covering the front surface of the silicon wafer substrate 501, and an anti-reflection layer 503 covering the surface of the doped layer 502 facing away from the silicon wafer substrate 501;
[0082] A back field 504 located on the back side of the silicon wafer substrate 501, the back field 504 has a hollow pattern;
[0083] A back passivation layer 505 located on the side of the back surface field 504 away from the silicon substrate 501, the back passivation layer 505 covering the back surface field 504 and the back surface of the silicon substrate 501;
[0084] a back electrode (not shown in the figure) located on the surface of the back passivation layer 505 facing away from the silicon substrate 501;
[0085] A positive electrode (not shown in the figure)...
PUM
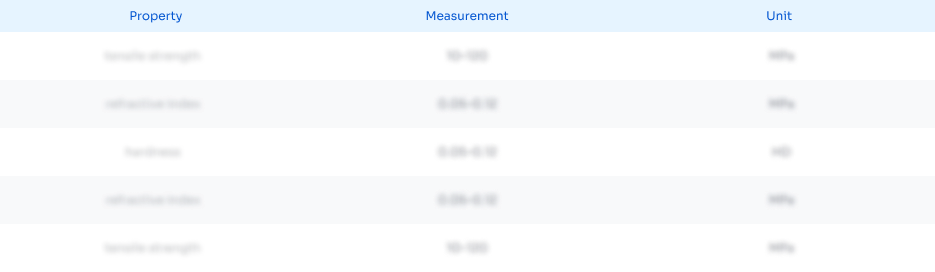
Abstract
Description
Claims
Application Information

- R&D
- Intellectual Property
- Life Sciences
- Materials
- Tech Scout
- Unparalleled Data Quality
- Higher Quality Content
- 60% Fewer Hallucinations
Browse by: Latest US Patents, China's latest patents, Technical Efficacy Thesaurus, Application Domain, Technology Topic, Popular Technical Reports.
© 2025 PatSnap. All rights reserved.Legal|Privacy policy|Modern Slavery Act Transparency Statement|Sitemap|About US| Contact US: help@patsnap.com