Alkylation reaction device and method
An alkylation reaction and an alkylation reactor technology, which is applied in the field of alkylation reaction devices, can solve the problems of poor acid-hydrocarbon mixing effect, atmosphericization space, and high reaction temperature, and achieves increased processing capacity and high operating flexibility. , the effect of large processing capacity
- Summary
- Abstract
- Description
- Claims
- Application Information
AI Technical Summary
Problems solved by technology
Method used
Image
Examples
Embodiment Construction
[0026] The present invention feeds low-carbon olefins and isobutane and liquid acid into the reactor. Low-carbon olefins include butene, propylene, pentene or olefin mixtures, and the preferred reaction materials are liquefied gas and isobutane after ether and concentrated sulfuric acid.
[0027] In the method of the present invention, the reactor packing is a structured packing with a cavity structure, and any structured packing that can form two disjoint intervals can be used, and corrugated packing and plate packing with a cavity structure are preferred here. The packed packing can be single-stage, two-stage or multi-stage, but multi-stage packing is preferred. There is space between each section of packing. Isobutane and concentrated sulfuric acid are fed to the first section of packing at the top of the reactor, and the liquefied gas after ether is divided into multiple feeds and enters the top of each section of packing.
PUM
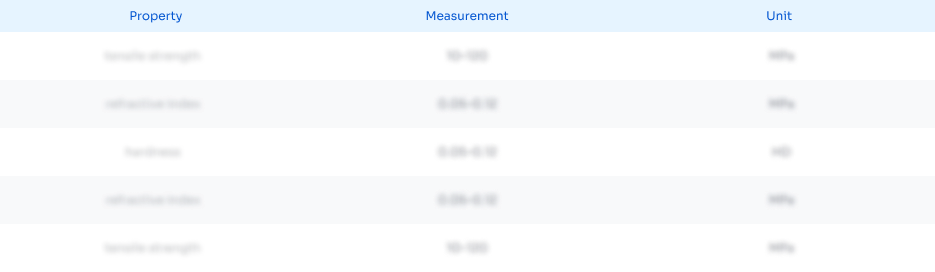
Abstract
Description
Claims
Application Information

- Generate Ideas
- Intellectual Property
- Life Sciences
- Materials
- Tech Scout
- Unparalleled Data Quality
- Higher Quality Content
- 60% Fewer Hallucinations
Browse by: Latest US Patents, China's latest patents, Technical Efficacy Thesaurus, Application Domain, Technology Topic, Popular Technical Reports.
© 2025 PatSnap. All rights reserved.Legal|Privacy policy|Modern Slavery Act Transparency Statement|Sitemap|About US| Contact US: help@patsnap.com