Vehicle thrust rod and assembly process thereof
An assembly process and thrust rod technology, applied in auxiliary devices, manufacturing tools, vehicle parts, etc., can solve the problems of increasing the overall weight of the product, manufacturing cost, heavy product weight, and high cost, and achieve weight reduction, beautiful welds, and connections. high intensity effect
- Summary
- Abstract
- Description
- Claims
- Application Information
AI Technical Summary
Problems solved by technology
Method used
Image
Examples
Embodiment
[0032] Example: such as Figure 1 to Figure 6 As shown, an automobile thrust rod includes a sleeve 1 and a thrust rod ball head 2. A ball joint 8 is also installed on the thrust rod ball head 2. The connecting part of the sleeve pipe 1 and the thrust rod ball head 2 The groove shape 3 is used to connect, and the thrust rod ball head 2 is a cylindrical structure. The groove shape 3 is connected by processing the two ends of the sleeve 1 to be connected with the thrust rod. The groove shape 3 intersecting the outer circle of the ball head 2 welds the bushing 1 and the thrust rod ball head 2 together. The bushing 1 and the ball head of the thrust rod 2 are connected through a groove shape 3, which can ensure that it meets the strength requirements of the product. The ball head of the thrust rod 2 has a cylindrical structure, thereby reducing the number of connections between the ball head of the thrust rod and the bushing in heat riveting, reducing the weight of the product and ...
PUM
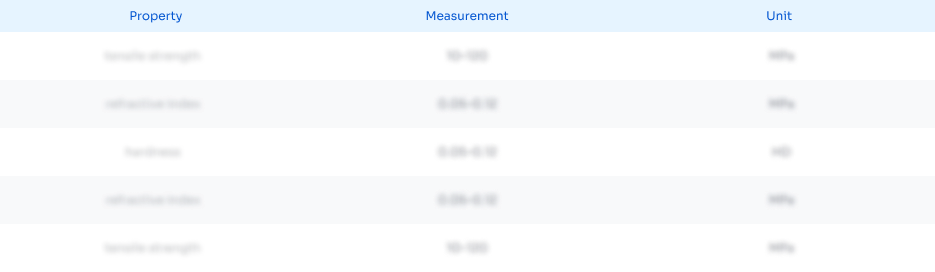
Abstract
Description
Claims
Application Information

- R&D
- Intellectual Property
- Life Sciences
- Materials
- Tech Scout
- Unparalleled Data Quality
- Higher Quality Content
- 60% Fewer Hallucinations
Browse by: Latest US Patents, China's latest patents, Technical Efficacy Thesaurus, Application Domain, Technology Topic, Popular Technical Reports.
© 2025 PatSnap. All rights reserved.Legal|Privacy policy|Modern Slavery Act Transparency Statement|Sitemap|About US| Contact US: help@patsnap.com