Preparation method of polyether modified polysiloxane foam stabilizer
A polysiloxane and polyether modification technology, which is applied to a preparation field of polyether modified polysiloxane, can solve the problem that the foam-stabilizing performance of the foam-stabilizing agent is unstable, and the foam-stabilizing effect of the foam-stabilizing agent is affected. The problem of high viscosity of foaming agent products can achieve the effects of easy control of the production process, stable structure and composition, and good foam uniformity.
- Summary
- Abstract
- Description
- Claims
- Application Information
AI Technical Summary
Problems solved by technology
Method used
Image
Examples
Embodiment 1
[0072] 1. Prepare allyl oxide ethylene oxide propylene oxide methyl ethers with different molecular weights respectively:
[0073] 1) Put 260kg of allyl alcohol and 4kg of sodium hydroxide into the reaction kettle, vacuumize at room temperature, and when the pressure reaches -0.095MPa, turn off the vacuum, start stirring, raise the temperature to 80°C, and slowly introduce 750kg of ethylene oxide and 990kg Propylene oxide, the temperature is controlled at 100-160 °C, after the feeding is completed, the aging reaction is performed until the pressure in the kettle is negative, and the reaction is stopped. Transfer the obtained allyl polyoxyethylene polyoxypropylene ether into the end-capped kettle, add 270kg of sodium hydroxide, and heat the reaction kettle to 60-80°C. After stirring for half an hour, replace it with nitrogen and then vacuumize it. The vacuum reaches - 0.095MPa, close the vacuum valve, slowly feed 270kg of methyl chloride, keep the temperature of the kettle betw...
Embodiment 2
[0082] 1. Prepare allyl oxide ethylene oxide propylene oxide methyl ethers with different molecular weights.
[0083] 1) Put 230kg of allyl alcohol and 6kg of sodium hydroxide into the reaction kettle quickly, vacuumize at room temperature, and when the pressure reaches -0.095MPa, turn off the vacuum, start stirring, raise the temperature to 80°C, and slowly introduce 760kg of ethylene oxide and 1010kg of propylene oxide, the temperature is controlled at 100-160°C, after the feeding is completed, the aging reaction is performed until the pressure in the kettle is negative, and the reaction is stopped, and the obtained allyl polyoxyethylene polyoxypropylene ether is transferred to the end-capping kettle, and 238kg of sodium hydroxide, the temperature of the reaction kettle is raised to 60-80°C, after stirring for half an hour, the vacuum is pumped after nitrogen replacement, the vacuum reaches -0.095MPa, the vacuum valve is closed, and 240kg of methyl chloride is slowly introduc...
Embodiment 3
[0093] 1. Prepare allyl oxide ethylene oxide propylene oxide methyl ethers with different molecular weights.
[0094] 1) Put 190kg of allyl alcohol and 6kg of sodium hydroxide into the reaction kettle quickly, vacuumize at room temperature, and when the pressure reaches -0.095MPa, turn off the vacuum, start stirring, raise the temperature to 80°C, and slowly introduce 780kg of ethylene oxide and 1030kg of propylene oxide, the temperature is controlled at 100-160 °C, after the feeding is completed, the aging reaction is until the pressure in the kettle is negative, and the reaction is stopped, and the obtained allyl polyoxyethylene polyoxypropylene ether is transferred to the end-capping kettle, adding 262kg of sodium hydroxide, the temperature of the reaction kettle is raised to 60-80°C, after stirring for half an hour, the vacuum is pumped after nitrogen replacement, the vacuum reaches -0.095MPa, the vacuum valve is closed, and 200kg of methyl chloride is slowly introduced, an...
PUM
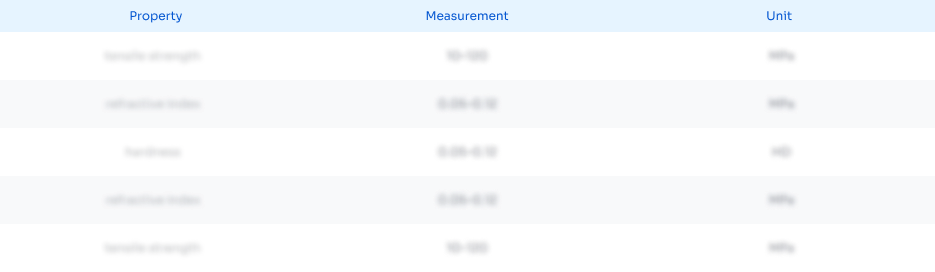
Abstract
Description
Claims
Application Information

- R&D
- Intellectual Property
- Life Sciences
- Materials
- Tech Scout
- Unparalleled Data Quality
- Higher Quality Content
- 60% Fewer Hallucinations
Browse by: Latest US Patents, China's latest patents, Technical Efficacy Thesaurus, Application Domain, Technology Topic, Popular Technical Reports.
© 2025 PatSnap. All rights reserved.Legal|Privacy policy|Modern Slavery Act Transparency Statement|Sitemap|About US| Contact US: help@patsnap.com