Single-oil passage pre-diaphragm type staggered plate primary combustion stage premixing and pre-vaporizing low-pollution combustor
A technology of combustion chamber and main combustion stage, which is applied in the direction of combustion chamber, continuous combustion chamber, combustion method, etc., to achieve the effect of improving uniformity, reducing pollution emissions and reducing pollution emissions
- Summary
- Abstract
- Description
- Claims
- Application Information
AI Technical Summary
Problems solved by technology
Method used
Image
Examples
Embodiment Construction
[0031] The present invention will be further described below in conjunction with the accompanying drawings and specific embodiments.
[0032] Figure 1-9 Disclosed is a premixed pre-evaporation low-pollution combustion chamber of a single-oil pre-film type staggered plate main combustion stage. Indoor casing 7, outer wall of flame tube 8, inner wall of flame tube 9 and combustion chamber head 13, diffuser 10 is welded together through inner and outer walls, casing 6 outside combustion chamber and casing 7 inside combustion chamber, outer wall of flame tube 8 The support plate at the rear edge is connected with the casing 6 outside the combustion chamber, and the inner wall 9 of the flame tube is also connected and fixed with the casing 7 inside the combustion chamber through the support plate at the rear; The mixing hole 11 is provided with a mixing hole 12 in the inner ring of the flame tube at the rear of the inner wall 9 of the flame tube. The mixing hole 11 enters the fl...
PUM
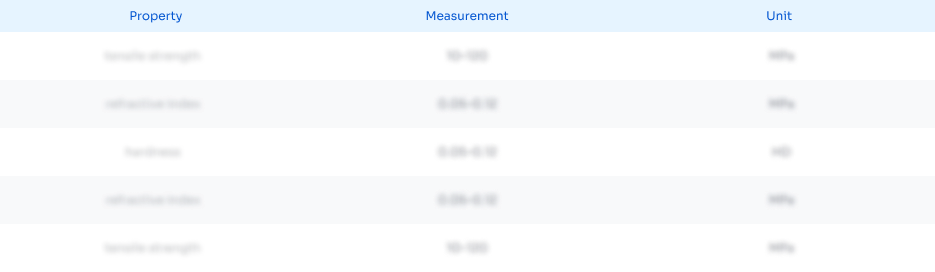
Abstract
Description
Claims
Application Information

- R&D Engineer
- R&D Manager
- IP Professional
- Industry Leading Data Capabilities
- Powerful AI technology
- Patent DNA Extraction
Browse by: Latest US Patents, China's latest patents, Technical Efficacy Thesaurus, Application Domain, Technology Topic, Popular Technical Reports.
© 2024 PatSnap. All rights reserved.Legal|Privacy policy|Modern Slavery Act Transparency Statement|Sitemap|About US| Contact US: help@patsnap.com