Kitchen knife blade manufacturing process
A preparation technology and blade technology, which is applied in the field of kitchen knife preparation technology, can solve the problems of low production efficiency and the like
- Summary
- Abstract
- Description
- Claims
- Application Information
AI Technical Summary
Problems solved by technology
Method used
Examples
Embodiment Construction
[0015] In Embodiment 1: when specifically producing blades, vanadium-titanium pig iron, scrap steel and returned materials are used for batching in a certain proportion, and are loaded into an induction melting furnace. The smelting temperature reaches 1500-1560°C, and two furnaces of molten iron that meet the composition requirements are smelted. The weight percentage of molten iron for blades is C: 3.85, Si: 0.95, Mn: 0.50, Mg: 0.25, Cr: 0.2, Mo: 0.10 , Cu: 0.25, Ti: 0.04, the balance is iron; the composition weight percentage of molten iron for the knife back is C: 3.75, Si: 0.95, Mg: 0.4, Cr: 0.5, and the balance is iron. Then pour into the insert cavity. Then put the blade into the heat treatment furnace, raise the temperature at a rate of 120-200°C / h, and raise the temperature to 820°C, perform austenitizing heat treatment, and keep it warm for 30 minutes. In the heat treatment furnace, only the blade is heated, and the back of the blade is separated from the blade by a...
PUM
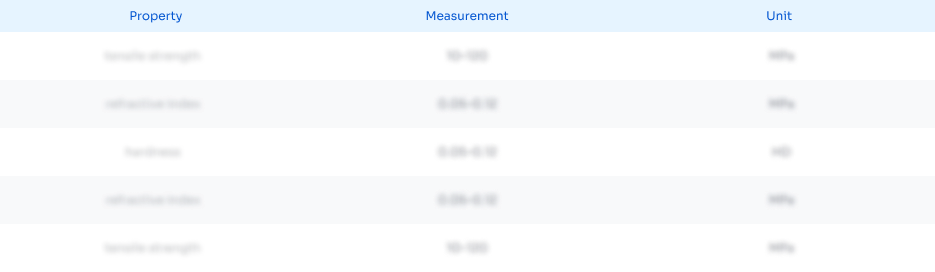
Abstract
Description
Claims
Application Information

- R&D Engineer
- R&D Manager
- IP Professional
- Industry Leading Data Capabilities
- Powerful AI technology
- Patent DNA Extraction
Browse by: Latest US Patents, China's latest patents, Technical Efficacy Thesaurus, Application Domain, Technology Topic, Popular Technical Reports.
© 2024 PatSnap. All rights reserved.Legal|Privacy policy|Modern Slavery Act Transparency Statement|Sitemap|About US| Contact US: help@patsnap.com