High frequency ultrahigh accelerating and decelerating micro-cutting motion control mechanism driven by gravity centre of linear motor
A linear motor and motion control technology, applied in the direction of drive devices, manufacturing tools, metal processing equipment, etc., can solve the problems of small continuous thrust of servo tool holders, affecting positioning and machining accuracy, affecting guide rail guiding accuracy, etc., and achieve large effective thrust , The consumption of inertial force is small, and the effect of ultra-high acceleration and deceleration cutting processing can be realized
- Summary
- Abstract
- Description
- Claims
- Application Information
AI Technical Summary
Problems solved by technology
Method used
Image
Examples
Embodiment Construction
[0027] Specific embodiments of the present invention will be described below in conjunction with the accompanying drawings.
[0028] In the accompanying drawings A. The center of gravity of the left limit position of the moving part of the present invention, B. the center of gravity of the right limit position of the moving part of the present invention; C. the center of gravity of the left limit position of the traditional mechanism, D. the center of gravity of the right limit position of the traditional mechanism, E. the return left of the traditional mechanism The center of gravity of the extreme position. Surface 1 and Surface 2 are non-overlapping spatial planes, A and B are collinear on Surface 1, C is on Surface 1, D is on Surface 2, and E and C are non-overlapping spatial points.
[0029] As shown in the figure, the controller, PWM driver, position signal detection element and linear motor unit form a closed-loop servo feedback system. The position signal detection el...
PUM
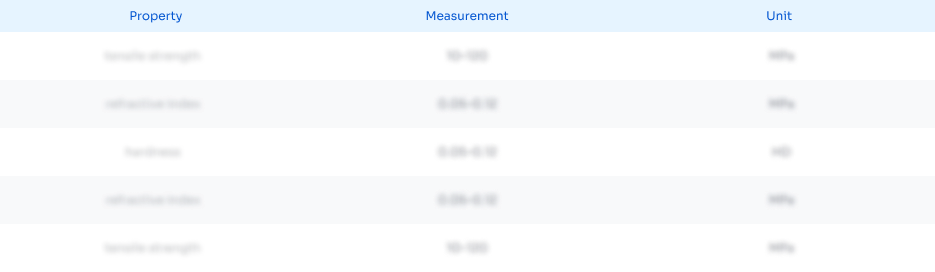
Abstract
Description
Claims
Application Information

- R&D
- Intellectual Property
- Life Sciences
- Materials
- Tech Scout
- Unparalleled Data Quality
- Higher Quality Content
- 60% Fewer Hallucinations
Browse by: Latest US Patents, China's latest patents, Technical Efficacy Thesaurus, Application Domain, Technology Topic, Popular Technical Reports.
© 2025 PatSnap. All rights reserved.Legal|Privacy policy|Modern Slavery Act Transparency Statement|Sitemap|About US| Contact US: help@patsnap.com