Method for manufacturing ultra-thin ruthenium film by aid of plasma enhanced atomic layer deposition process
An atomic layer deposition and plasma technology, applied in metal material coating process, superimposed layer plating, semiconductor/solid-state device manufacturing, etc., can solve the problem of poor step coverage, diffusion barrier layer and seed crystal copper layer. Difficulty shrinking, shrinking semiconductor device feature size, etc., to avoid voids
- Summary
- Abstract
- Description
- Claims
- Application Information
AI Technical Summary
Problems solved by technology
Method used
Image
Examples
Embodiment Construction
[0017] The method for preparing an ultra-thin ruthenium film by using a plasma-enhanced atomic layer deposition process proposed by the present invention includes: placing the substrate on which the ruthenium film needs to be grown into a reaction chamber, and heating the reaction chamber to 150° C. to 300° C., preferably Heating the reaction chamber to 250°C~270°C; then using the plasma-enhanced atomic layer deposition process to obtain a ruthenium film with a preset thickness by controlling the number of reaction cycles, wherein the ruthenium film is prepared by using the plasma-enhanced atomic layer deposition process A single reaction cycle consists of:
[0018] With bis (ethylcyclopentadienyl) ruthenium (II) (ie Ru (EtCp) 2 ) as the precursor, the Ru(EtCp) 2 Heating to 100°C~120°C, preferably Ru(EtCp) 2 Heat to 115°C and heat Ru(EtCp) 2 The obtained volatile gas is passed into the reaction chamber, and the passage time is 1 second to 10 seconds, and the preferred passa...
PUM
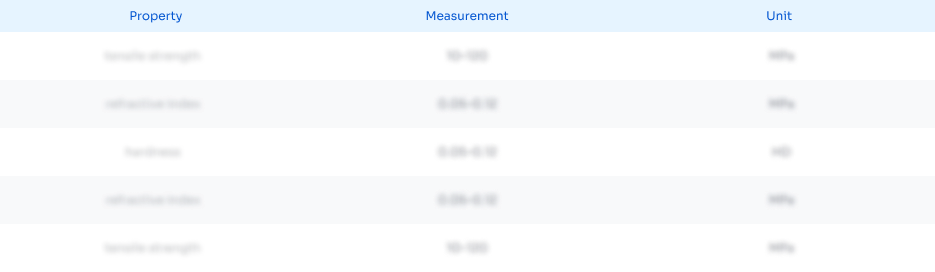
Abstract
Description
Claims
Application Information

- Generate Ideas
- Intellectual Property
- Life Sciences
- Materials
- Tech Scout
- Unparalleled Data Quality
- Higher Quality Content
- 60% Fewer Hallucinations
Browse by: Latest US Patents, China's latest patents, Technical Efficacy Thesaurus, Application Domain, Technology Topic, Popular Technical Reports.
© 2025 PatSnap. All rights reserved.Legal|Privacy policy|Modern Slavery Act Transparency Statement|Sitemap|About US| Contact US: help@patsnap.com