A Numerical Simulation Method for Low Velocity Impact Damage of Composite Laminates
A low-speed impact damage, composite material layer technology, applied in electrical digital data processing, special data processing applications, instruments, etc., can solve problems such as low computational efficiency, time-consuming and labor-intensive, inability to simulate delamination restrictions, etc. The effect of computing efficiency, shortening computing time, and reducing computing scale
- Summary
- Abstract
- Description
- Claims
- Application Information
AI Technical Summary
Problems solved by technology
Method used
Image
Examples
Embodiment Construction
[0024] The present invention will be described in further detail below in conjunction with the accompanying drawings, please refer to Figure 1 to Figure 6 .
[0025] A numerical simulation method for low-velocity impact damage of composite laminates, using Abaqus commercial software, including the following steps:
[0026] Step 1. Use the continuous shell unit SC8R to establish a single-layer laminate model with a unit size of H. The laminate contains multiple single-layer models, and the thickness of the single-layer model is the total thickness of multiple unidirectional prepreg tapes or woven fabrics with the same ply angle; figure 1 Shown
[0027] Step 2: Use the interface unit COH3D8 to establish an interlayer model of the laminate, the unit size is H / 5. The thickness of the interlayer model is one-thousandth of the thickness of the laminate model, and it is placed between two single-layer models to simulate interlayer delamination damage; figure 2 Shown
[0028] Step 3: Use ...
PUM
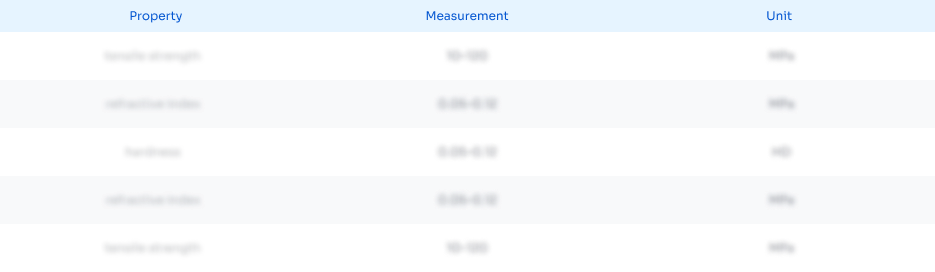
Abstract
Description
Claims
Application Information

- R&D
- Intellectual Property
- Life Sciences
- Materials
- Tech Scout
- Unparalleled Data Quality
- Higher Quality Content
- 60% Fewer Hallucinations
Browse by: Latest US Patents, China's latest patents, Technical Efficacy Thesaurus, Application Domain, Technology Topic, Popular Technical Reports.
© 2025 PatSnap. All rights reserved.Legal|Privacy policy|Modern Slavery Act Transparency Statement|Sitemap|About US| Contact US: help@patsnap.com