Polyurethane foam for wet-method preparation and preparation method thereof
A polyurethane foam and wet process technology, applied in the field of polyurethane foam production, can solve the problems that the sound absorption performance cannot meet the requirements of the main engine factory and the closed cell rate is high, and achieve the effect of uniform cells, increased foam rate, and reduced differences
- Summary
- Abstract
- Description
- Claims
- Application Information
AI Technical Summary
Problems solved by technology
Method used
Examples
Embodiment 1
[0038] (1) Configuration of part A material: Take 100 parts of polyether polyol, 0.5 part of glycerin, 0.1 part of cell opening agent, 0.1 part of antioxidant, put them into the mixer for pre-mixing, the speed of the mixer is 10rpm / min, and the mixing time is 50min to obtain the premixed A material;
[0039] Described polyether polyol composition is as follows:
[0040] Polyether A, sugar or sorbitol or glycerin, hydroxyl value 450, 10 parts;
[0041] Polyether B, phthalic anhydride polyester polyether, hydroxyl value 200, 5 parts;
[0042] Polyether C, glycerol polyether, polyether with a hydroxyl value of 28, 10 parts;
[0043] Polyether D, chain extender, hydroxyl value 56, 10 parts;
[0044] Polyether E, 3 parts of natural soybean polyether, hydroxyl value 20;
[0045] Polyether F, 1 part of hexamethylene diamine polyether, hydroxyl value 450;
[0046] Polyether G, glycerin, hydroxyl value 160, 10 parts.
[0047] The polyether polyol also includes 1 part of soybean o...
Embodiment 2
[0057] (1) Configuration of part A material: Take 100 parts of polyether polyol, 5 parts of glycerin, 2 parts of cell opener, 1.0 part of antioxidant, put them into the mixer for pre-mixing, the speed of the mixer is 20rpm / min, and the mixing time is 70min, obtain the premix A material;
[0058] Polyether A, glycerol, hydroxyl value 650, 30 parts;
[0059] Polyether B, phthalic anhydride polyester polyether, hydroxyl value 350, 35 parts;
[0060] Polyether C, glycerol polyether, polyether with a hydroxyl value of 35, 40 parts;
[0061] Polyether D, chain extender, hydroxyl value 160, 35 parts;
[0062] Polyether E, one of 30 parts of natural soybean polyether, palm oil polyether polyol or polymer polyether, the hydroxyl value is 56;
[0063] Polyether F, 10 parts of diamine polyether, hydroxyl value 800;
[0064] Polyether G, glycerin, hydroxyl value 240, 30 parts.
[0065] (2) Preparation of material B: material B is pure MDI or a mixture of polymeric MDI and MDI at a ra...
Embodiment 3
[0074] (1) Configuration of part A material: Take 100 parts of polyether polyol, 0.5-5 parts of glycerin, 0.1-2 parts of cell opener, 0.1-1.0 parts of antioxidant, put them into the mixer for pre-mixing, and the speed of the mixer is 10 -20rpm / min, the mixing time is 50-70min, to get the premix A material;
[0075] Polyether A, sorbitol, hydroxyl value 500, 20 parts;
[0076] Polyether B, phthalic anhydride polyester polyether, hydroxyl value 300, 20 parts;
[0077] Polyether C, glycerol polyether, polyether with a hydroxyl value of 30, 25 parts;
[0078] Polyether D, chain extender, hydroxyl value 100, 20 parts;
[0079] Polyether E, 15 parts palm oil polyether polyol, hydroxyl value 30;
[0080] Polyether F, 6 parts of diamine polyether, hydroxyl value 600;
[0081] Polyether G, glycerin, hydroxyl value 200, 20 parts.
[0082] (2) Preparation of material B: material B is a mixture of pure MDI or polymeric MDI and MDI at a ratio of 50-90: 50-10, which is also poured into...
PUM
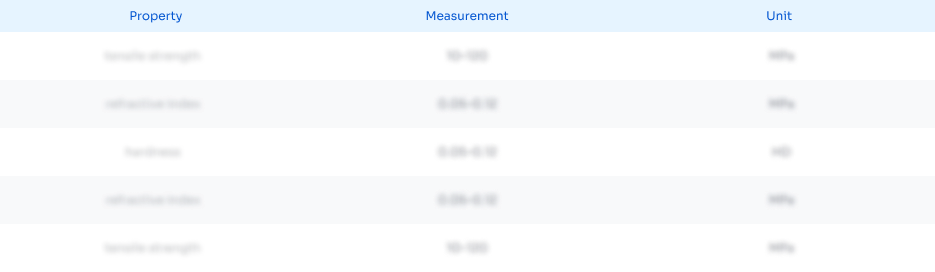
Abstract
Description
Claims
Application Information

- Generate Ideas
- Intellectual Property
- Life Sciences
- Materials
- Tech Scout
- Unparalleled Data Quality
- Higher Quality Content
- 60% Fewer Hallucinations
Browse by: Latest US Patents, China's latest patents, Technical Efficacy Thesaurus, Application Domain, Technology Topic, Popular Technical Reports.
© 2025 PatSnap. All rights reserved.Legal|Privacy policy|Modern Slavery Act Transparency Statement|Sitemap|About US| Contact US: help@patsnap.com