Coal drying device and drying method
A drying device and drying method technology, applied in drying solid materials, heating to dry solid materials, drying, etc., can solve the problems of catastrophic consequences, loss of coal volatiles, low gas-solid heat transfer efficiency, etc.
- Summary
- Abstract
- Description
- Claims
- Application Information
AI Technical Summary
Problems solved by technology
Method used
Image
Examples
Embodiment 1
[0033] figure 1 It is a structural schematic diagram of the coal drying device provided by Embodiment 1 of the present invention. The coal drying device provided by the present invention includes: a casing 1, at least three vibrating beds 2, and a radiant tube 3 with adjustable heating temperature; the inside of the casing 1 is isolated from the outside air; at least three vibrating beds 2 Arranged in a zigzag from top to bottom in the casing 1; each vibrating bed 2 is provided with a feeding port 4; each vibrating bed 2 is provided with the radiation tube 3 ; The heating temperature of the radiant tube 3 increases from top to bottom; wherein, the heating temperature of the radiant tube 3 at the bottom is 300°C-350°C.
[0034] In the coal drying device provided in the first embodiment, in the coal drying device provided above in the present invention, the coal drying device includes a casing 1, at least three vibrating beds 2, and a radiant tube 3 with adjustable heating temp...
Embodiment 2
[0036] see figure 1 as well as figure 2As shown, on the basis of the first embodiment above, the coal drying device provided by the second embodiment of the present invention also includes a water cooling jacket 5 and a distributor 6; the distributor 6 is located at the bottom of the vibration bed 2 Below the feeding port 4, and arranged in a zigzag shape with the vibrating bed 2 on the lowermost floor; the distributor 6 is provided with a plurality of lower leakage holes 7; the water cooling jacket 5 is located at the bottom of the distributor 6 Below, and in the water-cooling jacket 5, a plurality of cooling passages 8 extending vertically are formed; between the water-cooling jacket 5 and the distributor 6, a Sweeper 9.
[0037] In this second embodiment, since the temperature of the coal can reach 300°C-350°C when the coal is dried, in order to prevent the dry coal generated after the coal drying from burning at this temperature, it is necessary to lower the temperature...
Embodiment 3
[0042] figure 1 with image 3 It is a structural schematic diagram of the coal drying device provided by Embodiment 3 of the present invention. On the basis of the above-mentioned embodiment two, see figure 1 as well as image 3 As shown, in the coal drying device provided in the third embodiment, a water-cooled box 10 is also included; a water-cooled chamber 11 is formed in the water-cooled box 10 to communicate with the cooling channel 8 and the outside world; A screw pusher 12 for pushing the coal to the outside is also provided.
[0043] In the third embodiment, since the temperature of the dried coal needs to be rapidly lowered below the ignition point of the dried coal during the cooling process, in order to increase the cooling speed of the dried coal, a water-cooled box 10 is also added to the coal drying device. . The water-cooled box 10 forms a water-cooled chamber 11 that communicates with the cooling passage 8 and the outside world respectively. The side wall...
PUM
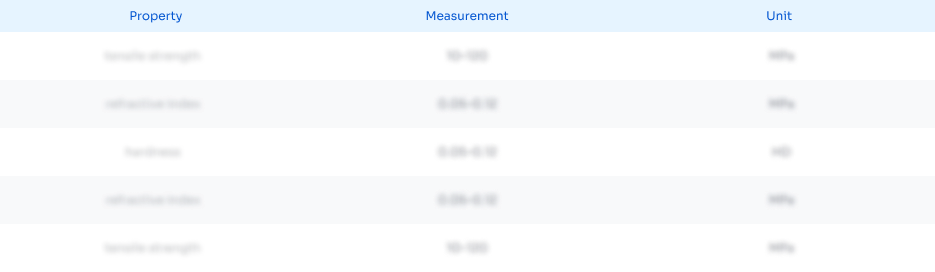
Abstract
Description
Claims
Application Information

- R&D
- Intellectual Property
- Life Sciences
- Materials
- Tech Scout
- Unparalleled Data Quality
- Higher Quality Content
- 60% Fewer Hallucinations
Browse by: Latest US Patents, China's latest patents, Technical Efficacy Thesaurus, Application Domain, Technology Topic, Popular Technical Reports.
© 2025 PatSnap. All rights reserved.Legal|Privacy policy|Modern Slavery Act Transparency Statement|Sitemap|About US| Contact US: help@patsnap.com