High strength anti-seismic reinforcing steel bar and production method thereof
A technology for anti-seismic steel bars and production methods, which is applied in the field of high-strength anti-seismic steel bars, and can solve problems such as unfavorable production and popularization of HRB500 high-strength steel bars, strict requirements on chemical composition and rolling temperature, and large consumption of vanadium or niobium alloys. To achieve the effects that are conducive to protection and rational utilization, promotion and application promotion, and strict control requirements
- Summary
- Abstract
- Description
- Claims
- Application Information
AI Technical Summary
Problems solved by technology
Method used
Examples
Embodiment 1
[0019] Step A: get the steel billet of following mass percentage chemical composition:
[0020] C: 0.22wt%, Si: 0.45wt%, Mn: 1.30wt%, V: 0.020wt%, N: 0.011wt%, Cr: 0.27wt%, Nb: 0.015wt%, S: 0.025wt%, P : 0.035wt%, the rest is Fe and unavoidable impurities;
[0021] Step B: Put the steel slab in step A into a heating furnace with a furnace temperature of 1200°C in the soaking section, heat for 90 minutes, and make the steel start rolling temperature reach 1040°C, and go through 6 passes of rough rolling and 5 passes of intermediate rolling , finish rolling for 6 passes, and control the final rolling temperature at 950°C;
[0022] Step C: Pass the steel bar in step B through the water cooling device quickly after final rolling, so that the surface temperature drops to 450°C, which is higher than the martensite formation temperature. After that, the temperature of the steel bar on the cooling bed is 690°C, and then Allow to cool naturally.
[0023] Step D: Naturally air-cool t...
Embodiment 2
[0027] Step A: get the steel billet of following mass percentage chemical composition:
[0028] C: 0.25wt%, Si: 0.50wt%, Mn: 1.35wt%, V: 0.023wt%, N: 0.013wt%, Cr: 0.30wt%, Nb: 0.015wt%, S: 0.020wt%, P : 0.025wt%, the rest is Fe and unavoidable impurities;
[0029] Step B: Send the billet of step A into a heating furnace with a furnace temperature of 1180°C in the soaking section, heat for 100 minutes, and make the steel start rolling temperature reach 1100°C, go through 6 passes of rough rolling and 4 passes of intermediate rolling , 6 passes of finishing rolling, and the temperature of finishing rolling is controlled at 980°C;
[0030] Step C: Pass the steel bars in step B through the water cooling device after final rolling, so that the surface temperature drops to 500°C, which is higher than the martensite formation temperature. After that, the temperature of the steel bars on the cooling bed is 700°C, and then Allow to cool naturally.
[0031] Step D: Naturally air-coo...
Embodiment 3
[0034] Step A: get the steel billet of following mass percent chemical composition:
[0035] C: 0.23wt%, Si: 0.60wt%, Mn: 1.45wt%, V: 0.025wt%, N: 0.012wt%, Cr: 0.36wt%, Nb: 0.017wt%, S: 0.030wt%, P : 0.035wt%, the rest is Fe and unavoidable impurities;
[0036]Step B: Send the steel slab from Step A into a heating furnace with a furnace temperature of 1200°C in the soaking section, and heat for 80 minutes to make the rolling start temperature of the steel reach 1100°C. After 6 passes of rough rolling and 4 passes of intermediate rolling , 4 passes of finishing rolling, and the temperature of finishing rolling is controlled at 980°C;
[0037] Step C: Pass the steel bar in step B through the water cooling device quickly after final rolling, so that the surface temperature drops to 500°C, which is higher than the martensite formation temperature. After that, the temperature of the steel bar on the cooling bed is 720°C, and then Allow to cool naturally.
[0038] Step D: Natura...
PUM
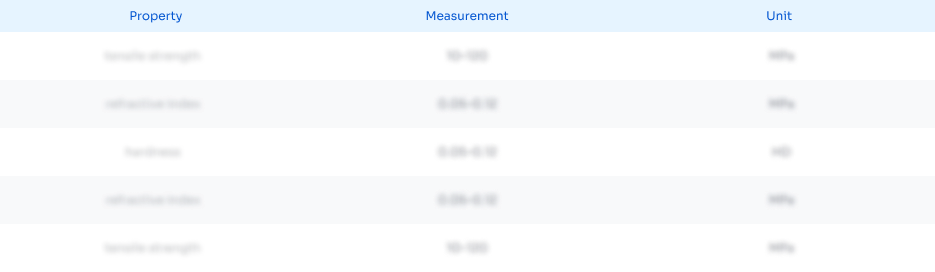
Abstract
Description
Claims
Application Information

- R&D
- Intellectual Property
- Life Sciences
- Materials
- Tech Scout
- Unparalleled Data Quality
- Higher Quality Content
- 60% Fewer Hallucinations
Browse by: Latest US Patents, China's latest patents, Technical Efficacy Thesaurus, Application Domain, Technology Topic, Popular Technical Reports.
© 2025 PatSnap. All rights reserved.Legal|Privacy policy|Modern Slavery Act Transparency Statement|Sitemap|About US| Contact US: help@patsnap.com