Hydraulic engineering driller
An engineering drilling rig, hydraulic technology, applied in the direction of rotary drilling rig, percussion drilling, rotary drilling, etc., can solve problems such as difficulty in tower installation, inconvenient movement and transfer, and difficulty in aligning hole positions, so as to achieve saving The effect of using cost and labor cost, optimizing equipment layout space, and simple and light equipment structure
- Summary
- Abstract
- Description
- Claims
- Application Information
AI Technical Summary
Problems solved by technology
Method used
Image
Examples
Embodiment Construction
[0034] figure 1 Is a schematic diagram of the structure of the present invention, figure 2 for figure 1 Top view of image 3 Schematic diagram of longitudinal walking mechanism, Figure 4 Is the longitudinal cross-sectional view of the horizontal traveling mechanism, Figure 5 Is a schematic diagram of the structure of the lateral walking mechanism, Image 6 It is a schematic diagram of the structure of the drill bit assembly, as shown in the figure: the hydraulic engineering drill of this embodiment includes a base 1, a column 42, a drilling assembly, a hydraulic drive system, and a power system;
[0035] The drilling assembly includes a drill bit assembly, a power head 26 and a guide tailstock 20. The drill bit assembly includes a drill bit 28 and a drill rod assembly 23. The end of the drill rod assembly 23 is set on the guide tailstock in a single degree of freedom in a circumferentially rotatable manner. 20. The structure can adopt the existing rotary joint structure, that i...
PUM
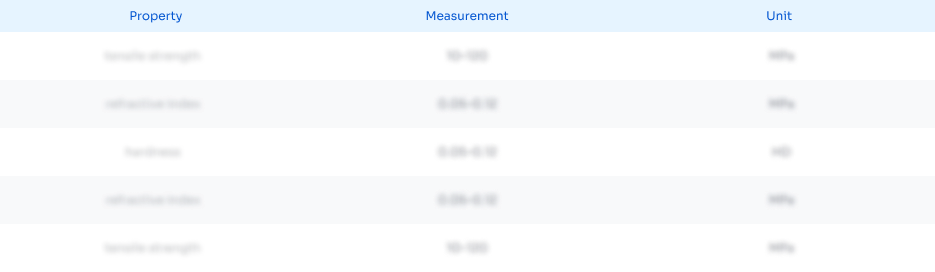
Abstract
Description
Claims
Application Information

- R&D
- Intellectual Property
- Life Sciences
- Materials
- Tech Scout
- Unparalleled Data Quality
- Higher Quality Content
- 60% Fewer Hallucinations
Browse by: Latest US Patents, China's latest patents, Technical Efficacy Thesaurus, Application Domain, Technology Topic, Popular Technical Reports.
© 2025 PatSnap. All rights reserved.Legal|Privacy policy|Modern Slavery Act Transparency Statement|Sitemap|About US| Contact US: help@patsnap.com