Lithium manganate battery cathode material recovery method
A technology of lithium manganate battery and positive electrode material is applied in the field of waste battery recycling, which can solve the problems of secondary pollution of waste acid or waste alkali, inability to guarantee waste, and large investment, and achieve the effect of broad application prospects.
- Summary
- Abstract
- Description
- Claims
- Application Information
AI Technical Summary
Problems solved by technology
Method used
Examples
Embodiment 1
[0030] Embodiment 1 adopts the inventive method to reclaim lithium manganate battery cathode material
[0031] Discharge the residual power of the waste lithium manganate power battery, disassemble the battery, take out the positive electrode, and recycle the battery case according to the classification of aluminum shell, steel shell, plastic, etc.; the positive electrode is heat-treated at 300°C, and then ball milled and sieved to separate the aluminum foil and the positive electrode Material mixture; the mixture is calcined at 1000°C and then pressed into balls.
[0032] Take 100kg of the mixture after pressing the ball, add 20kg of coke, 15kg of lime, and 16kg of silica, put it into an electric furnace for smelting for 2 hours, and cast it to obtain 70kg of manganese-silicon alloy. Lithium-containing solution was obtained by acid leaching the slag, and sodium carbonate solution was added to precipitate, and filtered to obtain 11 kg of lithium carbonate.
[0033] After test...
Embodiment 2
[0034] Embodiment 2 adopts the inventive method to reclaim lithium manganese oxide battery cathode material
[0035] Discharge the residual power of the waste lithium manganate power battery, disassemble the battery, take out the positive electrode, and recycle the battery case according to the classification of aluminum shell, steel shell, plastic, etc.; the positive electrode is heat-treated at 400°C, and then ball milled and sieved to separate the aluminum foil and the positive electrode Material mixture; the mixture is calcined at 1200°C and then pressed into balls.
[0036] Take 100kg of the mixture after pressing the ball, add 18kg of petroleum coke, 14kg of lime, and 17kg of silica, put it into an electric furnace for smelting for 1 hour, and cast it to obtain 68kg of manganese-silicon alloy. The slag was acid-leached to obtain a lithium-containing solution, and then a sodium carbonate solution was added for precipitation, and filtered to obtain 10 kg of lithium carbona...
Embodiment 3
[0038] Embodiment 3 adopts the inventive method to reclaim lithium manganate battery cathode material
[0039] Discharge the residual power of the waste lithium manganate power battery, disassemble the battery, take out the positive electrode, and recycle the battery case according to the classification of aluminum shell, steel shell, plastic, etc.; the positive electrode is heat-treated at 600°C, and then ball milled and sieved to separate the aluminum foil and the positive electrode Material mixture; the mixture is calcined at 1100°C and then pressed into balls.
[0040] Take 100kg of the mixture after pressing the ball, add 22kg of bituminous coal, 18kg of lime, and 13kg of silica, put it into an electric furnace for smelting for 3 hours, and cast it to obtain 71kg of manganese-silicon alloy. The slag was acid-leached to obtain a lithium-containing solution, and then a sodium carbonate solution was added for precipitation, and filtered to obtain 10 kg of lithium carbonate. ...
PUM
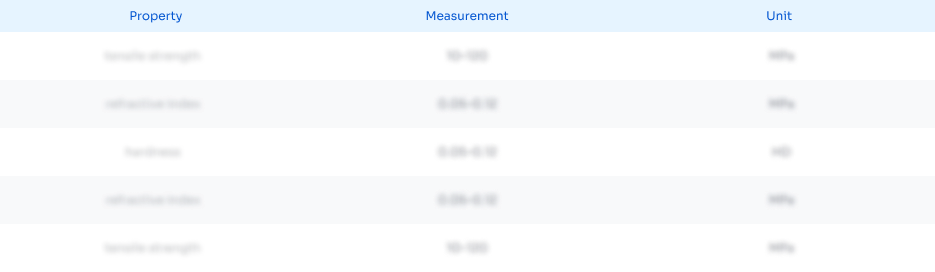
Abstract
Description
Claims
Application Information

- R&D Engineer
- R&D Manager
- IP Professional
- Industry Leading Data Capabilities
- Powerful AI technology
- Patent DNA Extraction
Browse by: Latest US Patents, China's latest patents, Technical Efficacy Thesaurus, Application Domain, Technology Topic, Popular Technical Reports.
© 2024 PatSnap. All rights reserved.Legal|Privacy policy|Modern Slavery Act Transparency Statement|Sitemap|About US| Contact US: help@patsnap.com