Method for handling stacked steel due to strip breakage on rolling mill
A treatment method and rolling mill technology, applied in the direction of metal rolling stand, metal rolling mill stand, metal rolling, etc., can solve the problems of small working space area, large amount of oil pollution in emulsion, and fire hazard, so as to improve production efficiency , Equipment safety and reliability guarantee, the effect of reducing labor intensity and working time
- Summary
- Abstract
- Description
- Claims
- Application Information
AI Technical Summary
Problems solved by technology
Method used
Examples
Embodiment Construction
[0016] Below, through the description of the embodiments, the specific embodiments of the present invention, such as the shape and structure of the various components involved, the mutual position and connection relationship between the various parts, the role and working principle of the various parts, etc. will be further described in detail:
[0017] The invention relates to a method for processing broken strip stacked steel in a rolling mill. The rolling mill includes multiple sets of work roll assemblies and multiple sets of intermediate roll assemblies. Each set of work roll assemblies includes two work rolls. Each set of work rolls A roll gap is formed between the two work rolls of the assembly. After the strip steel is rolled out through the roll gap between the work rolls, it is wound up by the take-up part. The processing steps of the rolling mill broken strip pile are as follows:
[0018] (1) When the above-mentioned rolling mill breaks and stacks steel, control the...
PUM
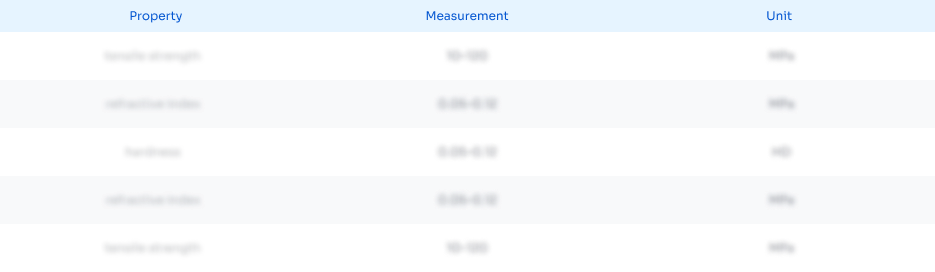
Abstract
Description
Claims
Application Information

- Generate Ideas
- Intellectual Property
- Life Sciences
- Materials
- Tech Scout
- Unparalleled Data Quality
- Higher Quality Content
- 60% Fewer Hallucinations
Browse by: Latest US Patents, China's latest patents, Technical Efficacy Thesaurus, Application Domain, Technology Topic, Popular Technical Reports.
© 2025 PatSnap. All rights reserved.Legal|Privacy policy|Modern Slavery Act Transparency Statement|Sitemap|About US| Contact US: help@patsnap.com