Machining method of circular transition section on bottom of central blind hole of generator rotor
A generator rotor and circular arc transition technology, which is applied in the manufacture of stator/rotor body and other directions, can solve the problems of easy generation of concentrated stress, failure to meet the accuracy requirements and performance requirements of the blind hole in the center of the rotor, and achieve the elimination of concentrated stress and meet the surface requirements. Effect of Roughness Requirements and Performance Requirements
- Summary
- Abstract
- Description
- Claims
- Application Information
AI Technical Summary
Problems solved by technology
Method used
Image
Examples
Embodiment Construction
[0032] The processing method of the circular arc transition section at the bottom of the central blind hole of the generator rotor of the present invention is used for processing such as figure 1 , figure 2 For the central blind hole of the generator rotor shown, the length of the central blind hole is not less than 1800 mm, the inner diameter is Ф120 (+0.4 / -0.2) mm, and the surface roughness is Ra1.6; the following steps are included:
[0033] The first step is to use a deep hole machine tool to nest materials on the workpiece with a nesting drill; then use a boring tool to rough and semi-finish the inner wall of the center hole to form a center hole with an inner diameter of Ф115-118mm; finally use Drill the plate to form a spherical bottom hole with a radius of 57-59mm; at this time, there will be obvious tool marks in the transition section between the center hole and the spherical bottom hole;
[0034] In the process of forming the spherical bottom hole, multiple plate ...
PUM
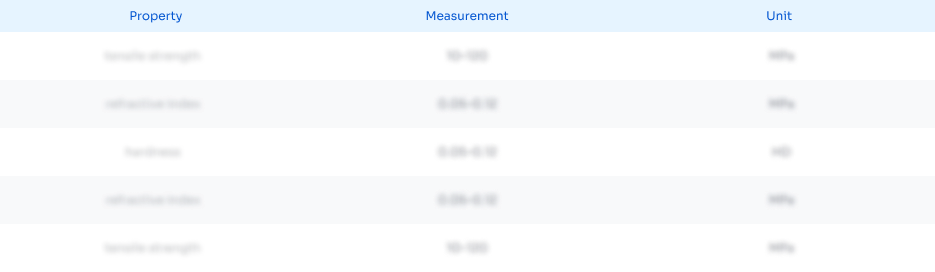
Abstract
Description
Claims
Application Information

- R&D Engineer
- R&D Manager
- IP Professional
- Industry Leading Data Capabilities
- Powerful AI technology
- Patent DNA Extraction
Browse by: Latest US Patents, China's latest patents, Technical Efficacy Thesaurus, Application Domain, Technology Topic, Popular Technical Reports.
© 2024 PatSnap. All rights reserved.Legal|Privacy policy|Modern Slavery Act Transparency Statement|Sitemap|About US| Contact US: help@patsnap.com