Multistage extrusion-type magneto-rheological damper
A magneto-rheological damper, squeeze-type technology, applied in the direction of vibration suppression adjustment, non-rotational vibration suppression, etc., can solve the problem of small damping force, achieve the effect of improving the damping force and increasing the effective working area
- Summary
- Abstract
- Description
- Claims
- Application Information
AI Technical Summary
Problems solved by technology
Method used
Image
Examples
Embodiment Construction
[0015] see figure 1 : the multi-stage extruded magnetorheological damper of the present invention is composed of upper end cover 1, outer cylinder body 2, magnetic isolation sleeve 3, upper limit spring 4, piston rod 5, sealing ring 6, sealing bolt 7, auxiliary piston Head 8, coil 9, working cavity 10, inner cylinder body 11, lower end cover 12, lower limit spring 13 and lower piston head 14 are formed. The lower end cover 12 is sequentially connected with a lower limit spring 13 , an inner cylinder 11 , a magnetic isolation sleeve 3 , a coil 9 and an outer cylinder 2 from the inside to the outside, and the upper end cover 1 is connected to the outer cylinder 2 . On the piston head 14, the inner cylinder body 11, the auxiliary piston head 8 and the upper end cover 1, a central hole is provided. The aperture of the inner cylinder body 11 central hole is greater than the diameter of the lower end of the piston rod, and the piston head 14 and the auxiliary piston head 8 are all c...
PUM
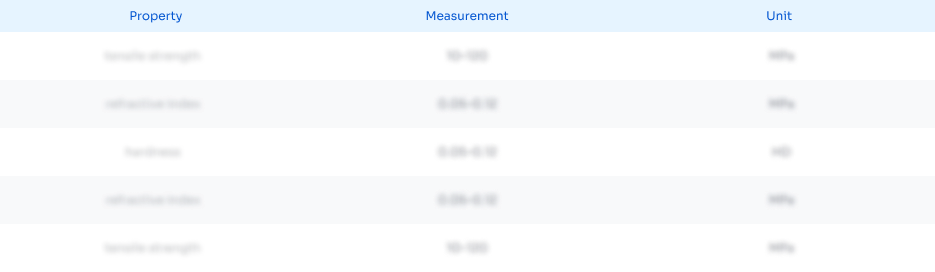
Abstract
Description
Claims
Application Information

- R&D
- Intellectual Property
- Life Sciences
- Materials
- Tech Scout
- Unparalleled Data Quality
- Higher Quality Content
- 60% Fewer Hallucinations
Browse by: Latest US Patents, China's latest patents, Technical Efficacy Thesaurus, Application Domain, Technology Topic, Popular Technical Reports.
© 2025 PatSnap. All rights reserved.Legal|Privacy policy|Modern Slavery Act Transparency Statement|Sitemap|About US| Contact US: help@patsnap.com