Method for designing post-process die profile machining data by draw piece scanning result
A technology of processing data and drawing process, which is applied in the field of first-order trimming molds after drawing, and can solve problems such as inconsistent profiles, unstable positioning, and air cutting
- Summary
- Abstract
- Description
- Claims
- Application Information
AI Technical Summary
Problems solved by technology
Method used
Image
Examples
Embodiment Construction
[0018] Below in conjunction with accompanying drawing and embodiment the present invention will be further described: as figure 1 As shown in Fig. 1, the drawn parts pressed after the drawing die is qualified are scanned to generate point cloud data and imported into the processing data environment (aligned with the position of the die). The profile of the mold is consistent with the theoretical model of the product. After drawing, the drawn profile A of the product has a certain deviation from the profile of the mold, which is mainly caused by the springback of the product. Therefore, the scanned point cloud data is used as a theoretical basis to carry out reverse design transformation and extend the processing data surface of each component to ensure the fitting and matching of the mold and the workpiece surface.
[0019] 1. After the die debugging of the drawing process is basically qualified, the final process parts are obtained through die stamping, laser cutting and othe...
PUM
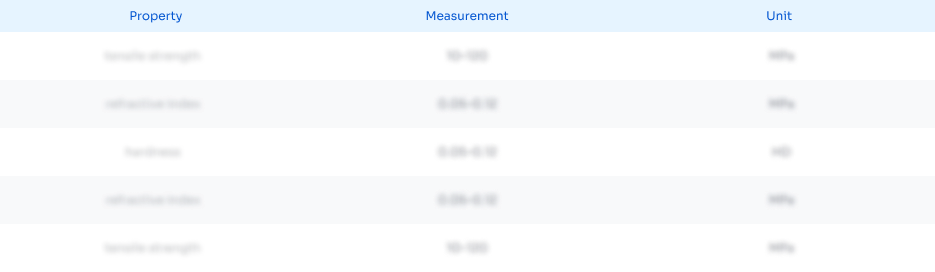
Abstract
Description
Claims
Application Information

- Generate Ideas
- Intellectual Property
- Life Sciences
- Materials
- Tech Scout
- Unparalleled Data Quality
- Higher Quality Content
- 60% Fewer Hallucinations
Browse by: Latest US Patents, China's latest patents, Technical Efficacy Thesaurus, Application Domain, Technology Topic, Popular Technical Reports.
© 2025 PatSnap. All rights reserved.Legal|Privacy policy|Modern Slavery Act Transparency Statement|Sitemap|About US| Contact US: help@patsnap.com