A kind of molding equipment and method of pulp molding
A technology of pulp molding and forming equipment, which is applied in the direction of textiles and papermaking, which can solve the problems of long process time and achieve the effect of improving production cycle and production cycle
- Summary
- Abstract
- Description
- Claims
- Application Information
AI Technical Summary
Problems solved by technology
Method used
Image
Examples
Embodiment 1
[0031] A kind of paper-plastic molding equipment of this embodiment, see figure 2 As shown, the sequence of preparation of pulp molded products includes: slurry suction mold 2, which forms a wet embryo after sucking slurry from pulp pool 1; extrusion mold 3 is arranged on the corresponding top of slurry suction mold 2, and After the pulp mold 2 is reversed upwards with the wet embryo, the wet embryo is first extruded with the extrusion mold 3; the hot pressing upper die 4 can move up and down in the vertical direction; the hot pressing lower die 5 can move left and right in the horizontal direction, when When moving to correspond up and down with the hot-pressing lower die 5, the wet embryo is subjected to hot-pressing treatment; the hot-pressing upper die 4 is provided with an air suction structure, and the hot-pressing lower die 5 is provided with an air-blowing structure; the hot-pressing lower die 5 and The transfer die 8 placed on the downstream side of the hot pressing ...
Embodiment 2
[0035] This embodiment provides a molding method of pulp molding, see Figure 5 shown, including the following steps:
[0036] After the pulp suction die 2 sucks the pulp from the pulp tank 1, it turns over, squeezes with the extrusion die 3 on it, and turns over again after extrusion. At this time, the hot pressing lower die 5 moves to the left to the pulp suction die 2 Below, the slurry suction mold 2 places the wet embryo in the hot-pressing lower mold 5, at this time, forming station 1, the hot-pressing lower mold 5 moves to the right to the position corresponding to the hot-pressing upper mold 4, forming a station Two, at this time, the hot-pressing upper die 4 moves vertically downward, extrudes the wet embryo with the hot-pressing lower die 5 and heats it to shape. There is a blowing structure, therefore, the molded product formed here is on the hot-pressing upper mold 4, and then the hot-pressing lower mold 5 and the transfer mold move to the left together, and return...
PUM
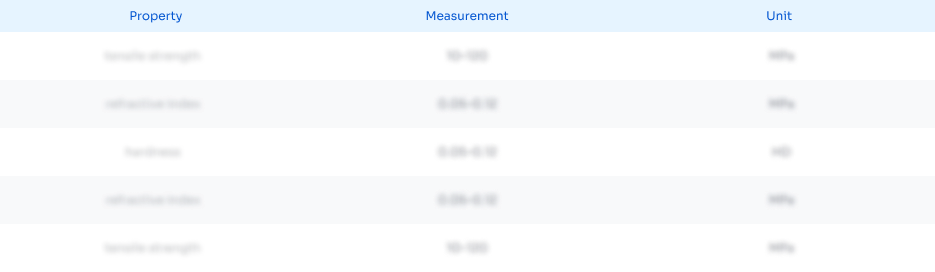
Abstract
Description
Claims
Application Information

- R&D Engineer
- R&D Manager
- IP Professional
- Industry Leading Data Capabilities
- Powerful AI technology
- Patent DNA Extraction
Browse by: Latest US Patents, China's latest patents, Technical Efficacy Thesaurus, Application Domain, Technology Topic, Popular Technical Reports.
© 2024 PatSnap. All rights reserved.Legal|Privacy policy|Modern Slavery Act Transparency Statement|Sitemap|About US| Contact US: help@patsnap.com