Vertical-structure LED (light emitting diode) production method utilizing multi-layer dielectric film reflection
A technology of light-emitting diodes and multi-layer dielectrics, applied in electrical components, circuits, semiconductor devices, etc., can solve the problems of affecting reflectivity, affecting light-extraction efficiency of light-emitting diodes, poor adhesion, etc.
- Summary
- Abstract
- Description
- Claims
- Application Information
AI Technical Summary
Problems solved by technology
Method used
Image
Examples
Embodiment Construction
[0023] The preparation steps of the inventive method are as follows:
[0024] ① First, if figure 1 As shown, a GaN-based epitaxial layer 101 is heteroepitaxially grown on a sapphire substrate 100, and the GaN-based epitaxial layer 101 sequentially includes an n-type GaN-based semiconductor layer, an active layer and a p-type GaN-based semiconductor layer from bottom to top.
[0025] ② if figure 2 As shown, the electron beam evaporation method is used to deposit a multilayer dielectric film 102 on the GaN-based epitaxial layer 101. The multilayer dielectric film 102 is made of SiO2 and TiO2, and the thicknesses are 75nm and 40nm respectively. The etching process exposes part of the surface of the p-type GaN semiconductor layer as a conductive channel.
[0026] ③ if image 3 As shown, the ohmic contact metal layer 103 is deposited on the surface of the multilayer dielectric film 102 and the exposed part of the p-type GaN semiconductor layer by electron beam evaporation meth...
PUM
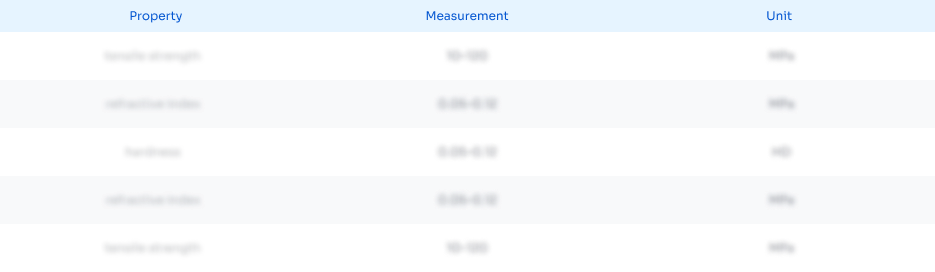
Abstract
Description
Claims
Application Information

- R&D Engineer
- R&D Manager
- IP Professional
- Industry Leading Data Capabilities
- Powerful AI technology
- Patent DNA Extraction
Browse by: Latest US Patents, China's latest patents, Technical Efficacy Thesaurus, Application Domain, Technology Topic, Popular Technical Reports.
© 2024 PatSnap. All rights reserved.Legal|Privacy policy|Modern Slavery Act Transparency Statement|Sitemap|About US| Contact US: help@patsnap.com