Glass rib splicing structure and construction method thereof
A construction method and glass rib technology, which can be applied to building components, building structures, walls, etc., can solve problems such as high maintenance costs, and achieve the effects of improving use safety, reducing thermal stress, and ensuring bonding firmness.
- Summary
- Abstract
- Description
- Claims
- Application Information
AI Technical Summary
Problems solved by technology
Method used
Image
Examples
Embodiment 1
[0034] Embodiment one: see Figure 2~4 As shown, a glass rib splicing structure includes an outer connecting plate 2 made of stainless steel covering both sides of the splicing ends of adjacent glass ribs 1, epoxy resin bonding between the outer connecting plates 2 on both sides and the middle glass rib 1 The adhesive layer 3 and the stainless steel pins 4 that run through the glass rib 1 and the outer connecting plates 2 on both sides, each section of the glass rib 1 on both sides of the splicing end, and between the adhesive layer 3 and the outer connecting plate 2 are respectively provided with a Inner steel plate 5.
[0035] Such as image 3 As shown, the two ends of the outer connecting plate 2 located on the adjacent glass rib 1 are respectively provided with flanges 6 to wrap the inner steel plate 5 inside, and a waterproof sealant is provided between the flange 6 and the glass rib 1 7. Prevent water seepage at the joint and ensure the firmness of the connection.
[...
PUM
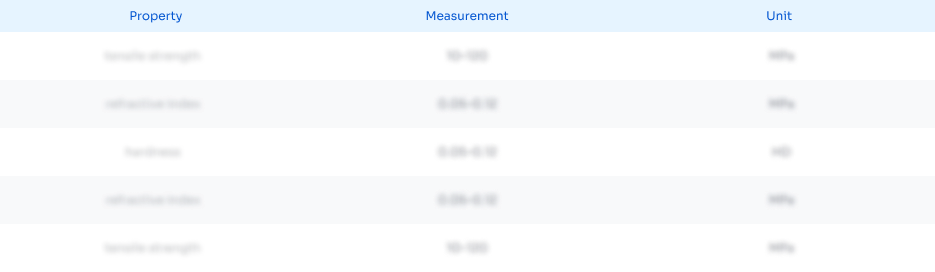
Abstract
Description
Claims
Application Information

- R&D
- Intellectual Property
- Life Sciences
- Materials
- Tech Scout
- Unparalleled Data Quality
- Higher Quality Content
- 60% Fewer Hallucinations
Browse by: Latest US Patents, China's latest patents, Technical Efficacy Thesaurus, Application Domain, Technology Topic, Popular Technical Reports.
© 2025 PatSnap. All rights reserved.Legal|Privacy policy|Modern Slavery Act Transparency Statement|Sitemap|About US| Contact US: help@patsnap.com