Power cable repairing adhesive tape and preparation method of the same
A technology for power cables and repair tapes, applied in adhesives, film/sheet adhesives, insulators, etc., can solve problems such as interface damage, bonding failure, poor low temperature resistance, etc., and achieve unique cold flow characteristics, The best sealing anti-corrosion, not easy to cure effect
- Summary
- Abstract
- Description
- Claims
- Application Information
AI Technical Summary
Problems solved by technology
Method used
Image
Examples
Embodiment 1
[0021] By weight percentage, butyl rubber (IIR268) 5%, high molecular weight polyisobutylene (PIB80) 8%; medium molecular weight polyisobutylene (PIB12) 30%; low molecular weight polyisobutylene (PIB) 15%; talcum powder 1250 mesh 40%; Antioxidant (1010) 1%; Phthalocyanine Green 1%.
[0022] The preparation method is as follows: Step A: Plasticize butyl rubber, high molecular weight polyisobutylene and medium molecular weight polyisobutylene, add low molecular weight polyisobutylene, add antioxidant and 1250 mesh talcum powder after mixing uniformly, and obtain Clay, kneader mixing temperature 130 + 15°C, kneading time 1 hour.
[0023] Step B: Transport the uniformly mixed cement to the reactor for secondary mixing through a single screw; the mixing temperature is 110 + 10°C for 0.5 hours.
[0024] Step C: Mix the cement through the reaction kettle and transport it to the discharge port of the extruder through the gear pump, extrude and coat it on the EPDM base material with...
Embodiment 2
[0026] By weight percentage, butyl rubber 10%; high molecular weight polyisobutylene 5%; medium molecular weight polyisobutylene 25%; low molecular weight polyisobutylene 10%; talcum powder 1250 mesh 48%; antioxidant 1010 1%; phthalocyanine green 1%
[0027] The preparation method is as follows: Step A: butyl rubber, high molecular weight polyisobutylene and medium molecular weight polyisobutylene are mixed, then low molecular weight polyisobutylene is added, after mixing evenly, antioxidant and talcum powder are added, after mixing evenly, the cement is obtained, kneaded Machine mixing temperature 130 + 15°C, kneading time 1.5 hours.
[0028] Step B: Transport the uniformly mixed cement to the reactor for secondary mixing through a single screw; the mixing temperature is 110 + 10°C for 0.5 hours.
[0029] Step C: Mix the cement through the reaction kettle and transport it to the discharge port of the extruder through the gear pump, extrude and coat it on the EPDM base mater...
Embodiment 3
[0031] By weight percentage, including: butyl rubber 7%; high molecular weight polyisobutylene 8%; medium molecular weight polyisobutylene 28%; low molecular weight polyisobutylene 10%; light calcium 1250 mesh 46%; antioxidant 1010 0.5%; phthalocyanine green 0.5 %
[0032] The preparation method is as follows: Step A: Mix butyl rubber, high-molecular-weight polyisobutylene and medium-molecular-weight polyisobutylene, then add low-molecular-weight polyisobutylene, add antioxidant and light calcium after mixing uniformly, and obtain cement after mixing uniformly. Kneader mixing temperature 130 + 15°C, kneading time 1 hour.
[0033] Step B: Transport the uniformly mixed cement to the reactor for secondary mixing through a single screw; the mixing temperature is 110 + 10°C for 0.5 hours.
[0034] Step C: Mix the cement through the reaction kettle and transport it to the discharge port of the extruder through the gear pump, extrude and coat it on the EPDM base material with a th...
PUM
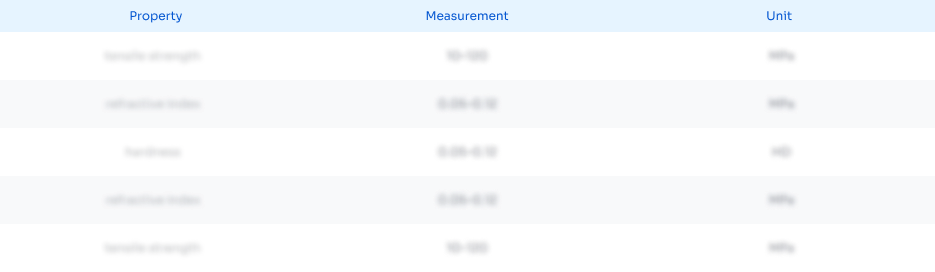
Abstract
Description
Claims
Application Information

- R&D
- Intellectual Property
- Life Sciences
- Materials
- Tech Scout
- Unparalleled Data Quality
- Higher Quality Content
- 60% Fewer Hallucinations
Browse by: Latest US Patents, China's latest patents, Technical Efficacy Thesaurus, Application Domain, Technology Topic, Popular Technical Reports.
© 2025 PatSnap. All rights reserved.Legal|Privacy policy|Modern Slavery Act Transparency Statement|Sitemap|About US| Contact US: help@patsnap.com