House heat-insulation coating and preparation method thereof
A technology for thermal insulation coatings and houses, applied in cement coatings, lime coatings, coatings, etc., can solve the problems of increasing the thickness of walls, increasing the load of thermal insulation performance of aerated concrete blocks, etc., to prevent condensation water , to prevent the effect of mold on the wall
- Summary
- Abstract
- Description
- Claims
- Application Information
AI Technical Summary
Problems solved by technology
Method used
Examples
Embodiment 1
[0018] (1) Mixing ratio of raw materials:
[0019] High alumina cement: lime: fly ash: water glass = 0.3: 0.2: 0.45: 0.05, then add water and stir according to the water-to-material ratio of 0.56. Wherein the foaming agent (aluminum powder) is used in an amount of 0.085% (percentage by weight) of the total amount of air-entrained concrete materials, and is stirred in a reaction kettle to form a viscous paste. The coating is solidified at room temperature for 10-24 hours after use. It can be applied directly to the new wall without pointing; as the insulation layer, the outer cement mortar protective layer is used, and the service life is the same as that of the building; if it is used on the old building, the exterior wall paint needs to be polished and then applied.
Embodiment 2
[0021] (1) Mixing ratio of raw materials:
[0022] High alumina cement: lime: fly ash: water glass = 0.32: 0.21: 0.42: 0.05, then add water and stir according to the water-to-material ratio of 0.56. Wherein the consumption of foaming agent (aluminum powder) is 0.086% (percentage by weight) of the total amount of materials. , Stir in the reactor to make a viscous paste. The coating is solidified at room temperature for 10-24 hours after use. It can be applied directly to the new wall without pointing; as the insulation layer, the outer cement mortar protective layer is used, and the service life is the same as that of the building; if it is used on the old building, the exterior wall paint needs to be polished and then applied.
Embodiment 3
[0024] (1) Mixing ratio of raw materials:
[0025] High alumina cement: lime: fly ash: gypsum = 0.31: 0.22: 0.43: 0.04 and then add water and stir according to the water-material ratio of 0.58. Wherein the consumption of foaming agent (aluminum powder) is 0.085% (percentage by weight) of the total amount of materials. , Stir in the reactor to make a viscous paste. The coating is solidified at room temperature for 10-24 hours after use. It can be applied directly to the new wall without pointing; as the insulation layer, the outer cement mortar protective layer is used, and the service life is the same as that of the building; if it is used on the old building, the exterior wall paint needs to be polished and then applied.
PUM
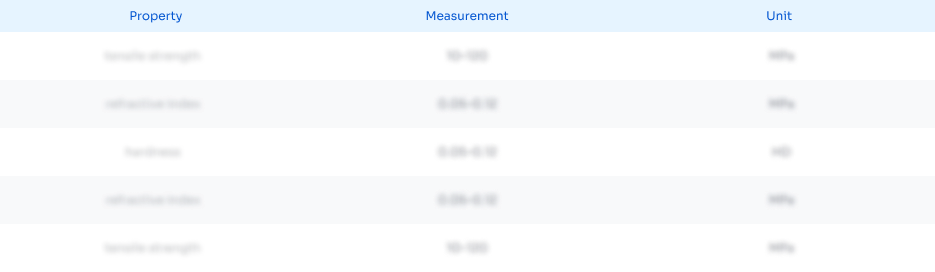
Abstract
Description
Claims
Application Information

- R&D
- Intellectual Property
- Life Sciences
- Materials
- Tech Scout
- Unparalleled Data Quality
- Higher Quality Content
- 60% Fewer Hallucinations
Browse by: Latest US Patents, China's latest patents, Technical Efficacy Thesaurus, Application Domain, Technology Topic, Popular Technical Reports.
© 2025 PatSnap. All rights reserved.Legal|Privacy policy|Modern Slavery Act Transparency Statement|Sitemap|About US| Contact US: help@patsnap.com