Utilization method for hydrocarbon fuel gas rich in alkyne
A technology for hydrocarbon fuels and alkynes, applied in the fields of hydrogenation to hydrocarbons, organic chemistry, etc., can solve problems such as ineffective utilization and burning, improve operability and safety, improve overall efficiency, and avoid waste of resources Effect
- Summary
- Abstract
- Description
- Claims
- Application Information
AI Technical Summary
Problems solved by technology
Method used
Image
Examples
Embodiment 1
[0019] according to figure 1 As shown, adopting the technical process of the present invention, the feed is a hydrocarbon material rich in alkynes, and a nickel-palladium-copper multi-metal catalyst is used in a selective hydrogenation reactor; the reaction temperature is 45°C, the reaction pressure is 2.0MPa, and the hydrocarbon material The volumetric space velocity is 2.5 hours-1, the molar ratio of hydrogen to alkyne is 1.5:1, and the first-stage hydrogenation reactor is a bubbling bed. The second-stage selective hydrogenation reactor adopts nickel-molybdenum multi-metal catalyst; the reaction temperature is 160°C, the reaction pressure is 2.5MPa, the volume space velocity of hydrocarbon material is 1 hour-1, and the molar ratio of hydrogen to alkyne is 450:1. The stage hydrogenation reactor is a fixed bed,
[0020] The test proves that the alkyne conversion rate is about 98.1%, and the composition of the main components in and out is shown in the following table 1:
[0...
Embodiment 2
[0023] according to figure 1 As shown, adopting the technological process of the present invention, the feedstock is a hydrocarbon material rich in alkynes, and a nickel-palladium-copper multi-metal catalyst is used in a selective hydrogenation reactor; the reaction temperature is 67°C, the reaction pressure is 2.0MPa, and the hydrocarbon material The volumetric space velocity is 4 hours-1, the molar ratio of hydrogen to alkyne is 3.5:1, and the first-stage hydrogenation reactor is a bubbling bed. The second-stage selective hydrogenation reactor adopts nickel-molybdenum multi-metal catalyst; the reaction temperature is 180°C, the reaction pressure is 2.5MPa, the volume space velocity of hydrocarbon material is 2 hours-1, and the molar ratio of hydrogen to alkyne is 550:1. The stage hydrogenation reactor is a fixed bed.
[0024] The test proves that the alkyne conversion rate is about 97.5%, and the composition of the main components in and out is shown in Table 2 below:
[0...
PUM
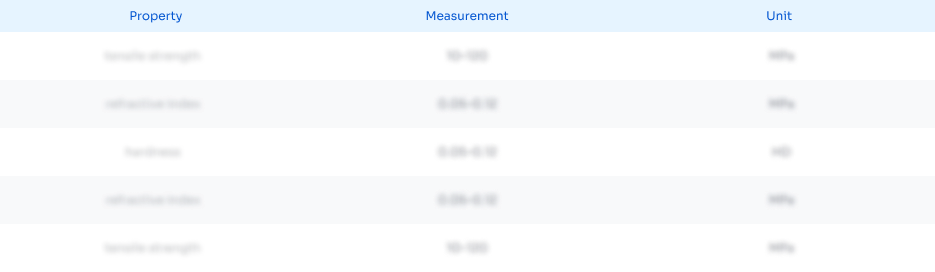
Abstract
Description
Claims
Application Information

- Generate Ideas
- Intellectual Property
- Life Sciences
- Materials
- Tech Scout
- Unparalleled Data Quality
- Higher Quality Content
- 60% Fewer Hallucinations
Browse by: Latest US Patents, China's latest patents, Technical Efficacy Thesaurus, Application Domain, Technology Topic, Popular Technical Reports.
© 2025 PatSnap. All rights reserved.Legal|Privacy policy|Modern Slavery Act Transparency Statement|Sitemap|About US| Contact US: help@patsnap.com