Numerical control machining method of aero-engine disc-shaft integrated structure part
A technology for aero-engine and structural parts, which is applied in the field of numerical control machining of aero-engine disc-shaft integrated structural parts, can solve the problems of low qualification rate of parts, many toolings, long processing cycle of parts, etc., and achieves reduction of processing cycle, quality improvement, production Efficiency improvement effect
- Summary
- Abstract
- Description
- Claims
- Application Information
AI Technical Summary
Problems solved by technology
Method used
Image
Examples
Embodiment 1
[0012] This embodiment provides a numerical control machining method for an aero-engine disc-shaft integral structure part, which is characterized in that: the aero-engine disc-shaft integral structure part numerical control machining method is as follows:
[0013] The wall thickness tolerance of the part's web plate and the connection between the journal and the disc body is 0.05mm, the precision hole diameter tolerance is 0.015mm, the relative reference position is Φ0.05mm, and the end face of the web plate and the inner hole relative to the reference verticality and runout are both 0.01mm; Main processing steps: die forging→rough machining of the big end→rough machining of the small end→vacuum stress relief heat treatment→finishing of the profile of the big end→finishing of the small end. A total of 4 processes are required, and 2 sets of special fixtures are required; The turning-milling compound machining center replaces the original ordinary lathe, CNC lathe and five-coor...
Embodiment 2
[0016] This embodiment provides a numerical control machining method for an aero-engine disc-shaft integral structure part, which is characterized in that: the aero-engine disc-shaft integral structure part numerical control machining method is as follows:
[0017] The wall thickness tolerance of the part's web plate and the connection between the journal and the disc body is 0.05mm, the precision hole diameter tolerance is 0.015mm, the relative reference position is Φ0.05mm, and the end face of the web plate and the inner hole relative to the reference verticality and runout are both 0.01mm; Main processing steps: die forging→rough machining of the big end→rough machining of the small end→vacuum stress relief heat treatment→finishing of the profile of the big end→finishing of the small end. A total of 4 processes are required, and 2 sets of special fixtures are required; The turning-milling compound machining center replaces the original ordinary lathe, CNC lathe and five-coor...
Embodiment 3
[0020] This embodiment provides a numerical control machining method for an aero-engine disc-shaft integral structure part, which is characterized in that: the aero-engine disc-shaft integral structure part numerical control machining method is as follows:
[0021] The wall thickness tolerance of the part's web plate and the connection between the journal and the disc body is 0.05mm, the precision hole diameter tolerance is 0.015mm, the relative reference position is Φ0.05mm, and the end face of the web plate and the inner hole relative to the reference verticality and runout are both 0.01mm; Main processing steps: die forging→rough machining of the big end→rough machining of the small end→vacuum stress relief heat treatment→finishing of the profile of the big end→finishing of the small end. A total of 4 processes are required, and 2 sets of special fixtures are required; The turning-milling compound machining center replaces the original ordinary lathe, CNC lathe and five-coor...
PUM
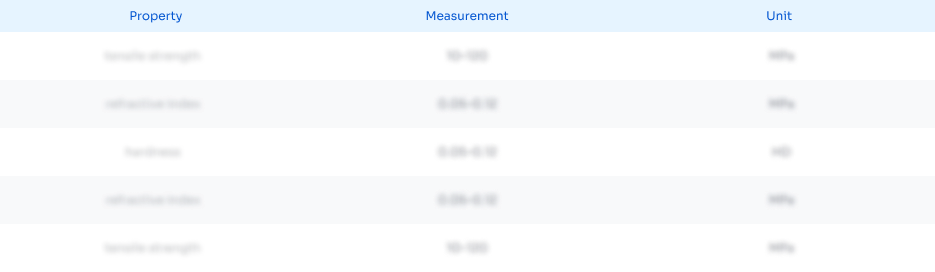
Abstract
Description
Claims
Application Information

- R&D Engineer
- R&D Manager
- IP Professional
- Industry Leading Data Capabilities
- Powerful AI technology
- Patent DNA Extraction
Browse by: Latest US Patents, China's latest patents, Technical Efficacy Thesaurus, Application Domain, Technology Topic, Popular Technical Reports.
© 2024 PatSnap. All rights reserved.Legal|Privacy policy|Modern Slavery Act Transparency Statement|Sitemap|About US| Contact US: help@patsnap.com