Metal carrier and manufacturing method of metal carrier
A technology of metal carrier and manufacturing method, which is applied in the direction of catalyst carrier, catalyst carrier, chemical instrument and method, etc., can solve the problems of metal carrier shedding, cost increase, performance decline, etc., and achieve the effect of preventing deformation and preventing the decline of purification performance
- Summary
- Abstract
- Description
- Claims
- Application Information
AI Technical Summary
Problems solved by technology
Method used
Image
Examples
no. 1 Embodiment approach
[0040] Next, a first embodiment of the present invention will be described with reference to the drawings. FIG. 1 is a perspective view showing the structure of a metal carrier according to this embodiment.
[0041]As shown in FIG. 1 , the metal carrier 1 of the present embodiment is formed by laminating metal belt-shaped corrugated foils 2 and flat foils 3 , rolling them into a spiral shape, and then winding them on the outer periphery. The brazing foil is pressed into the metal casing 4, and the corrugated foil 2 and the flat foil 3 are diffusely bonded by heating in a vacuum state, and these foils and the casing 4 are brazed to form a metal casing. Carrier 1.
[0042] Here, the shape of the corrugated foil 2 at the end of the roll of the metal carrier 1 will be described with reference to FIG. 2 . As shown in FIG. 2, by gradually expanding the wave pitch of the corrugated foil 2 with wave height A, the wave height is reduced to B. The wave height B is 1 / 3 to 1 / 4 of the w...
no. 2 Embodiment approach
[0056] Next, a method of manufacturing a metal carrier according to a second embodiment will be described with reference to the drawings. FIG. 7 is a diagram showing the configuration of a processing device for gradually reducing the wave height of the corrugated foil 2 . As shown in FIG. 7 , the processing device 71 has a die 73 formed with grooves 72 a to 72 g for fixing the wave tops of the corrugated foil 2 , and punches 74 a to 74 g for inserting the wave troughs of the corrugated foil 2 . However, as a mechanism for lowering the punches 74a to 74g, a general method such as a method using a cam mechanism or a method using an actuator can be used.
[0057] In the processing device 71 constituted in this way, FIG. 7 shows the state before processing, and grooves 72a to 72g are prepared on the die 73 at the positions of the processed state according to the number of crests of the corrugated foil 2 .
[0058] On the other hand, the punches 74a to 74g have a shape correspondi...
no. 3 Embodiment approach
[0064] Next, a method of manufacturing a metal carrier according to a third embodiment will be described with reference to the drawings. 11 to 13 are diagrams showing the structure of a processing device for gradually reducing the wave height of the corrugated foil 2. FIG. 11 is a front view, FIG. 12 is a plan view from above, and FIG. Side view of the corrugated foil in the upper state.
[0065] As shown in FIGS. 11 and 12 , the processing device 81 has a die 82 formed to have the shape of the corrugated foil 2 when it is completed, an elevator 83 for placing the corrugated foil 2 , and a pin 84 inserted into the trough of the corrugated foil 2 . , a block member 85 holding the pin 84 , a holding bolt 86 connecting the block members 85 , a spring 87 biasing the pin 84 , and a punch 88 formed in the shape of the corrugated foil 2 at the time of completion.
[0066] In the processing apparatus 81 configured in this way, the corrugated foil 2 is placed on the lifter 83 provided...
PUM
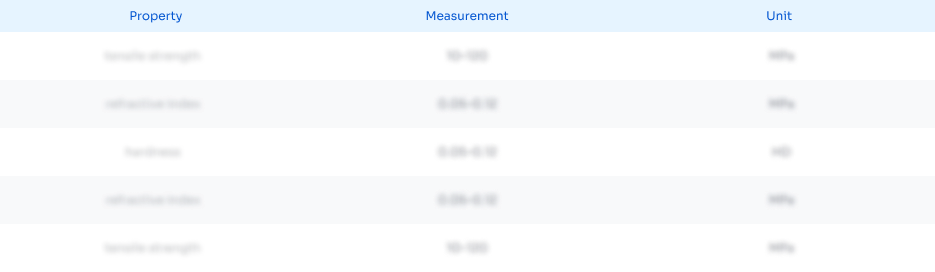
Abstract
Description
Claims
Application Information

- R&D
- Intellectual Property
- Life Sciences
- Materials
- Tech Scout
- Unparalleled Data Quality
- Higher Quality Content
- 60% Fewer Hallucinations
Browse by: Latest US Patents, China's latest patents, Technical Efficacy Thesaurus, Application Domain, Technology Topic, Popular Technical Reports.
© 2025 PatSnap. All rights reserved.Legal|Privacy policy|Modern Slavery Act Transparency Statement|Sitemap|About US| Contact US: help@patsnap.com