Clean wastepaper deinking production method
A waste paper deinking and clean production technology, applied in the field of papermaking, can solve the problems of high chemical consumption and pollution, and achieve the effects of high biological activity, reduced material consumption, and mild conditions
- Summary
- Abstract
- Description
- Claims
- Application Information
AI Technical Summary
Problems solved by technology
Method used
Examples
Embodiment 1
[0021] Embodiment 1: 8# U.S. waste newsprint (8# U.S. waste) deinking
[0022] (1) Pulping: Add 8# American waste newsprint into the pulper, add 0.02% alkaline lipase, 0.1% sodium hydroxide, 0.01% surfactant (cocoic acid monoethanolamide sulfo The mass ratio of disodium succinate monoester to fatty acid potassium soap is 1:1), the pulping concentration is controlled to 15%, the disintegration is 20min, and the temperature is 55°C.
[0023] (2) Flotation: Flotation is carried out in a flotation tank. Dilute the disintegrated slurry to a slurry concentration of 1%, control the ventilation rate at 25-35L / h, and the pressure at 0.3-1M Pa. Flotation at room temperature for 15 minutes.
[0024] (3) Washing: After flotation, the pulp is diluted with water to a concentration of 0.2%, and washed through a 120-mesh copper mesh. All of the above are based on 100Kg of dry pulp.
[0025] After collecting the deinked pulp, make a sheet on a standard paper former (quantitatively 200g / m 2 ...
Embodiment 2
[0030] (1) Pulping: Add Hong Kong waste newsprint into the pulper, add 0.02% alkaline lipase, 0.1% sodium hydroxide, 0.01% surfactant: cocoic acid monoethanolamide sulfosuccinic acid The mass ratio of monoester disodium to fatty acid potassium soap is 1:1, the pulping concentration is controlled at 15%, the disintegration is 20min, and the temperature is 55°C.
[0031] (2) Flotation: Flotation is carried out in a flotation tank. Dilute the disintegrated slurry to a slurry concentration of 1%, control the ventilation rate at 25-35L / h, and the pressure at 0.3-1M Pa. Flotation at room temperature for 15 minutes.
[0032] (3) Washing: After flotation, the pulp is diluted with water to a concentration of 0.2%, and washed through a 120-mesh copper mesh. All of the above are based on 100Kg of dry pulp.
[0033] After collecting the deinked pulp, make a sheet on a standard paper former (quantitatively 200g / m 2 ), measure the degree of dust, whiteness, residual ink, and calculate the...
Embodiment 3
[0038] (1) Pulping: Add 8# American waste newsprint into the pulper, add 0.02% alkaline lipase and cellulase 1:1 composition, 0.1% sodium hydroxide, 0.01% surface activity Agent: Potassium monododecyl phosphate, control pulp concentration 15%, disintegrate for 20min, temperature 55℃.
[0039] (2) Flotation: Flotation is carried out in a flotation tank. Dilute the disintegrated slurry to a slurry concentration of 1%, control the ventilation rate at 25-35L / h, and the pressure at 0.3-1M Pa. Flotation at room temperature for 15 minutes.
[0040] (3) Washing: After flotation, the pulp is diluted with water to a concentration of 0.2%, and washed through a 120-mesh copper mesh. All of the above are based on 100Kg of dry pulp.
[0041] After collecting the deinked pulp, make a sheet on a standard paper former (quantitatively 200g / m 2 ), measure the degree of dust, whiteness, residual ink, and calculate the yield. Whiteness and Residual Ink Concentration (ERIC) were measured by Tech...
PUM
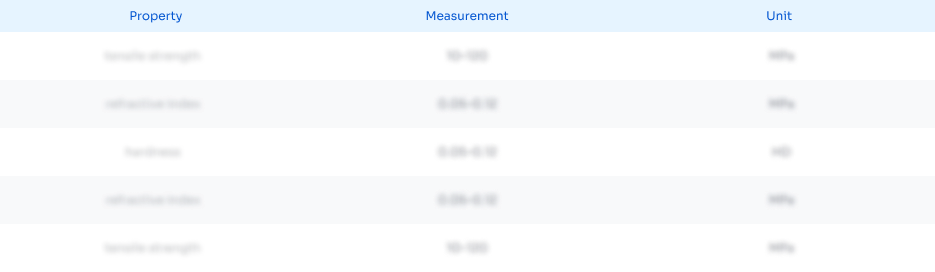
Abstract
Description
Claims
Application Information

- R&D
- Intellectual Property
- Life Sciences
- Materials
- Tech Scout
- Unparalleled Data Quality
- Higher Quality Content
- 60% Fewer Hallucinations
Browse by: Latest US Patents, China's latest patents, Technical Efficacy Thesaurus, Application Domain, Technology Topic, Popular Technical Reports.
© 2025 PatSnap. All rights reserved.Legal|Privacy policy|Modern Slavery Act Transparency Statement|Sitemap|About US| Contact US: help@patsnap.com