Super-durable and super-hydrophobic textile and its making method
A textile and super-hydrophobic technology, applied in textiles, papermaking, fiber treatment, etc., can solve the problems of poor durability of super-hydrophobic performance, weak binding force between nanoparticles and fiber matrix, easy loss of super-hydrophobicity of fabrics, etc., to achieve durability The effect of chemical solution corrosion
- Summary
- Abstract
- Description
- Claims
- Application Information
AI Technical Summary
Problems solved by technology
Method used
Image
Examples
Embodiment 1
[0015] Step 1: Treat polyester fabric with alkali: first wash the polyester fabric with deionized water, dry it for later use, then immerse the fabric in sodium hydroxide with a concentration of 400-450g / L, and the concentration of accelerator 1227 is 0.5~4g / L The finishing liquid is then steamed, and the fabric is taken out after steaming, fully washed with deionized water, and dried to obtain an alkali-treated polyester fabric.
[0016] Step 2: Dip 3g of alkali-treated polyester fabric into 1.26g of cetyltrimethoxysilane and 0.6g of PDMS (polydimethylsiloxane), 0.06g of low surface energy silicone elastomer curing agent In the hydrophobic finishing solution, soak for a certain period of time, treat at 80°C for 3 minutes, take out the fabric and dry it at 135°C for 0.5h. The surface contact angle of the obtained fabric is 160.7 °, after the obtained fabric is worn 2000 times on the AATCC color fastness to rubbing tester, its contact angle with water droplets is 150.3 °, and t...
Embodiment 2
[0018] Step 1: Treat polyester fabric with alkali: first wash the polyester fabric with deionized water, dry it for later use, then immerse the fabric in sodium hydroxide with a concentration of 400-450g / L, and the concentration of accelerator 1227 is 0.5~4g / L In the finishing solution, take out the fabric after steaming, fully wash and dry with deionized water. An alkali-treated polyester fabric is obtained.
[0019] Step 2: Dip 3g of alkali-treated polyester fabric into 1.38g of dodecyltriethoxysilane, 0.6g of PDMS, and 0.06g of silicone elastomer curing agent in a low surface energy hydrophobic finishing solution for a certain period of time , treated at 80°C for 3min, took out the fabric and baked at 135°C for 0.5h. The surface contact angle of the obtained fabric is 158.1 °, after the obtained fabric is worn 2000 times on the AATCC color fastness tester, its contact angle with water droplets is 151.7 °, and the fabric is put into 200mL of 0.37% Add 10 pieces of 6mm stee...
Embodiment 3
[0021] Step 1: Treat polyester fabric with alkali: first wash the polyester fabric with deionized water, dry it for later use, then immerse the fabric in sodium hydroxide with a concentration of 400-450g / L, and the concentration of accelerator 1227 is 0.5~4g / L In the finishing solution, take out the fabric after steaming, fully wash and dry with deionized water. An alkali-treated polyester fabric is obtained.
[0022] Step 2: immerse 3g of alkali-treated polyester fabric in 1.5g of cetyltrimethoxysilane, 0.6g of PDMS, and 0.06g of silicone elastomer curing agent in a low-surface-energy hydrophobic finishing solution for a certain period of time. Treat at 80°C for 3min, take out the fabric and bake at 135°C for 0.5h. The surface contact angle of the obtained fabric is 162.1 °, after the obtained fabric is worn 2000 times on the AATCC color fastness tester to rubbing, its contact angle with water droplets is 154.5 °, and the fabric is put into 200mL of 0.37% Add 10 pieces of 6...
PUM
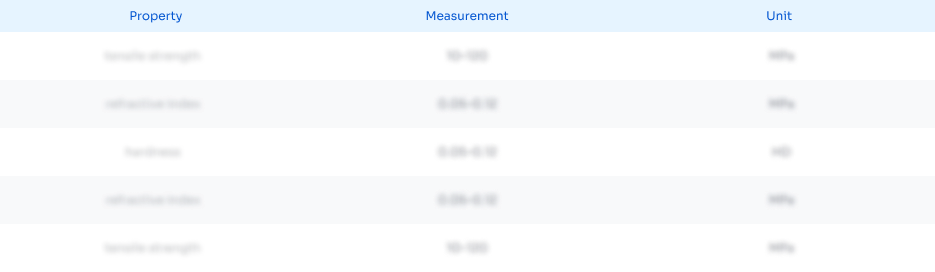
Abstract
Description
Claims
Application Information

- Generate Ideas
- Intellectual Property
- Life Sciences
- Materials
- Tech Scout
- Unparalleled Data Quality
- Higher Quality Content
- 60% Fewer Hallucinations
Browse by: Latest US Patents, China's latest patents, Technical Efficacy Thesaurus, Application Domain, Technology Topic, Popular Technical Reports.
© 2025 PatSnap. All rights reserved.Legal|Privacy policy|Modern Slavery Act Transparency Statement|Sitemap|About US| Contact US: help@patsnap.com